Давайте честно, в нашей легкой промышленности не так и много предприятий, которые смогли отметить свой 90-летний юбилей, да ещё и чувствовать себя на рынке весьма уверенно, задавая темп и для других игроков. Сегодня речь пойдёт о компании Юничел, что родом из Челябинска, и мы с вами посмотрим, как они делают обувь для нас. Они стабильно входят в тройку крупнейших производителей обуви в нашей стране. Представляете, ежегодно с конвейеров фабрики сходит порядка 3 млн пар обуви высокого качества. При этом более 10% всей кожаной обуви, выпускаемой в настоящее время в России, сделано на Юничел.

2. А тут сразу становится понятно, что ты попал в обувное царство.
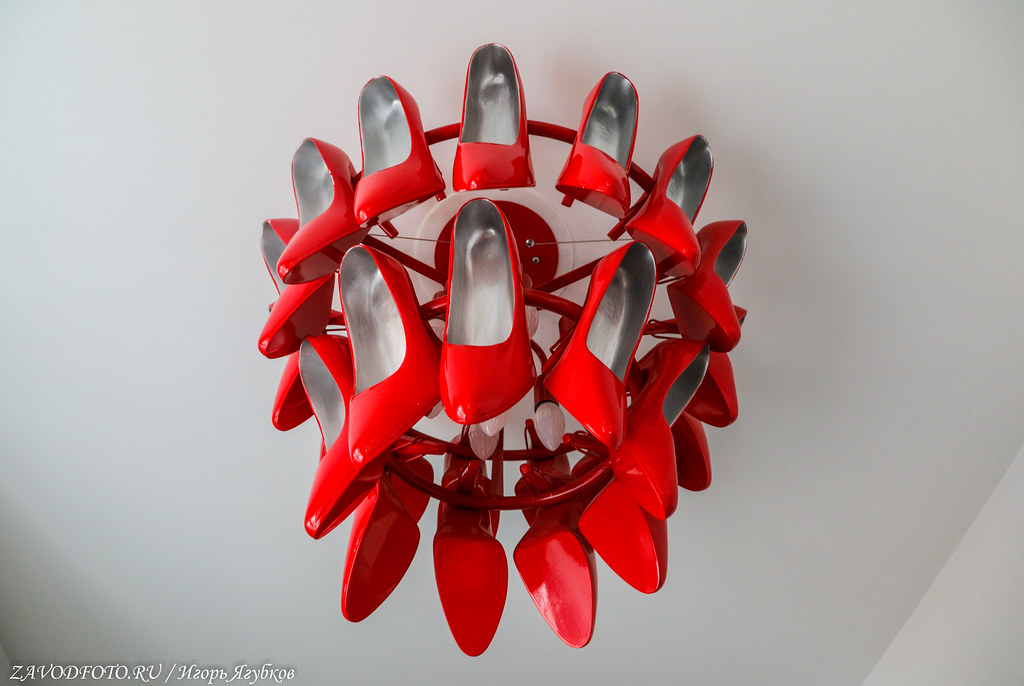
Эх, просто обожаю такие ретро-мозайки. Пожалуй, тогда с истории и начнём. Итак, в 1932 году в Челябинске на основании приказа Управления «Кожснабсбыта» в районе ЧТЗ, во втором бараке, была организована сапожно-пошивочная мастерская №4. Поначалу обувь там шилась вручную из текстиля и брезента с применением деревянных подошв. Тогда в мастерской работали всего 16 человек, а объёмы производства обуви не превышали десятка пар в день. Из оборудования была только машинка Singer с ножным приводом. Шли годы, дело росло, уже в 40-е годы они наладили производство модельной обуви. Ее разрабатывали по модным журналам Москвы и Ленинграда. Кстати, мозаики в лестничных пролётах сохранены и поддерживаются по сей день с тех пор, как обувная фабрика переехала в это здание, в 1968 году.
3.

А вот и главный дизайнер фабрики, Храмцова Инна. Она нам похвасталась, что у них недавно появилась супер-пупер итальянская программа для 3D-моделирования обуви. Уникальная и единственная в России! Ну, значит теперь точно не пропадём :). Ведь самый широкий ассортимент среди наших производителей обуви именно у них, - мужская женская, школьная, дошкольная обувь, модели для спорта и отдыха на природе, трекинговая обувь, всех размеров для всех сезонов. Дизайн обуви - это тонкий, творческий, но вместе с тем математически точный процесс создания и конструирования модели дизайнером. Сначала создается эскиз. Раньше дизайнерам нужно было разложить этот эскиз на детали, выкроить из бумаге, потом склеить на колодке, подогнать, чтоб бумажная модель «сидела» идеально, а потом оцифровать получившиеся детали. После чего они отправлялись на раскрой. Теперь весь это процесс происходит автоматизирован, как раз в этой в специальной 3D-программе. Модель, подбор цвета кожи, формы подошвы и фурнитура подбирается виртуально. Такую модель на специальном планшете можно покрутить и посмотреть. Виртуальная готовая модель сама «раскладывается» на детали, информация о которых передается на раскройные машины, где оптимально раскладывает детали на кожине и кроит уже лазер! Новые коллекции создаются два раза в год: весенне-летняя и осенне-зимняя. Разработка любой коллекции начинается за год до того, как она появляется на полках магазинов. То есть в этом году решают, что будет носить покупатель в следующем. Ежемесячно модельеры и дизайнеры придумывают около 100-150 моделей обуви. Все они отшиваются и проходят через художественный совет. Модели, которые прошли кастинг, запускаются в серийное производство. Каких именно и сколько решают на ежегодных ярмарках, куда Юничел приглашает всех заинтересованных представителей магазинов. В среднем на такой обувной суд компания готовит примерно 800 моделей. По итогу и составляется производственный план на ближайшие полгода.
4.
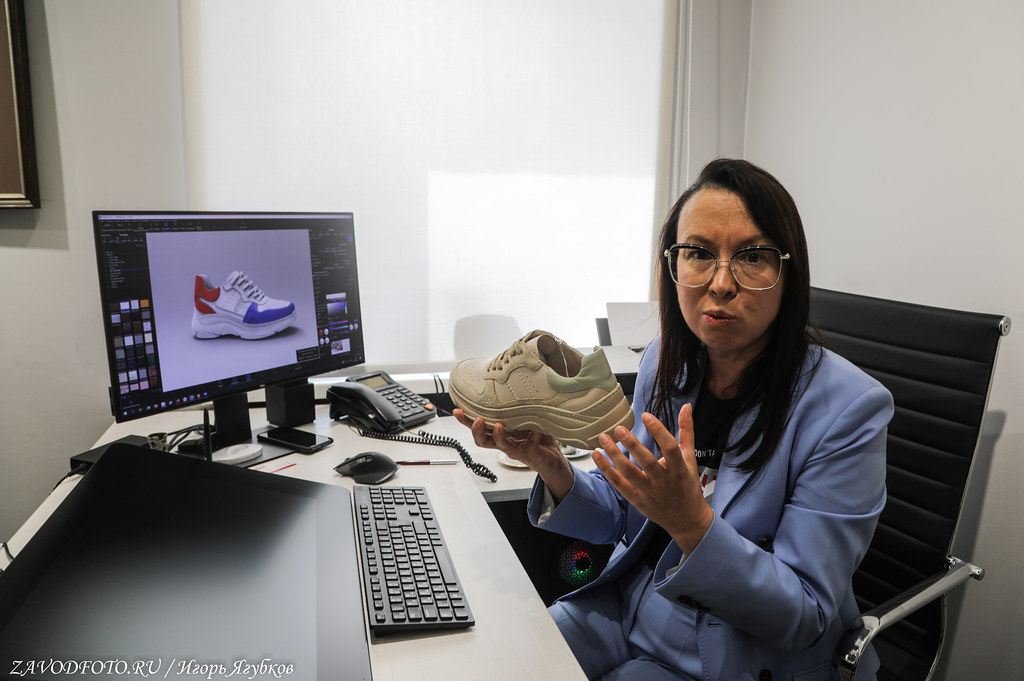
5. И переходим, собственно, на производство. Раскройный цех. Здесь происходит раскрой сырья. Первыми нас встречают гидравлические прессы. В цехе порядка 75 прессов, которые совершают до 3200 ударов за смену, чтобы вырезать союзку, берцы, голенище, штаферку и другие детали для сбора будущей пары обуви.

6. Одна модель обуви может состоять из 40 и более деталей. Все они производятся здесь: верх, подклад, межподклад - каждый участок в цехе отвечает за свою часть и от каждого в равной степени зависит качество готовой обуви.

Вернемся к истории. Великая Отечественная война. В ноябре 1941 года в Челябинск эвакуировали Харьковскую обувную фабрику. Ей выделили помещения на первом этаже жилого дома. Через некоторое время она была переименована в Челябинскую обувную фабрику №1 модельной обуви. Да как и на других предприятиях того времени многие сотрудники ушли на фронт, им же на смену пришли подростки 13-17 лет. Тогда на фабрике работало порядка 120-150 человек.
7.

Когда пришло мирное время, внимания к нашей фабрике ещё прибавилось. Как сейчас говорят, началась консолидация обувщиков в регионе. Вначале в 1957 году Челябинские обувные фабрики №2 и №3 были объединены в одну. А еще через три года - в 1960 году Совнархоз постановил объединить обувные фабрики №1 и №2, на базе которых и была организована Челябинская обувная фабрика. К этому времени объемы производства значительно выросли, а численность сотрудников достигла 881 человека. Теперь продукция с маркой Челябинской обувной фабрики продавалась не только на Урале, но и во Владивостоке, Архангельске, Ашхабаде.
8.

В начале 1961 года была выбрана площадка в районе Северо-запада города и начато проектирование новой фабрики. Как результат, в 1968 году было сдано в эксплуатацию новое здание фабрики, которое было построено всего за 10 месяцев. Предприятие было оборудовано новейшей советской и зарубежной техникой. 9 января 1968 года с конвейера сходят первые пары обуви. При этом самая первая пара была отправлена в Москву председателю совета Министров товарищу Косыгину.
9. Благодаря таким резакам и получаются нужные заготовки.

Новый толчок для роста был достигнут благодаря созданию Челябинского производственного объединения, соединившее специализированные обувные предприятия в Челябинске, Магнитогорске, Троицке, Златоусте и Кыштыме. К концу 60-х годов ЧПОО вышло по объему производства обуви на 3 место в РСФСР и на 5 место в СССР. В 1975 году при обувном объединении создан фирменный магазин «Башмачок». Здесь не только продавали обувь, но и устраивали показы и обсуждения моделей с покупателями. Это был первый в стране Дом моделей промышленного типа, главной задачей которого была разработка промышленных коллекций обуви для потоков фабрик Челябинского объединения и нескольких предприятий Роскожобувьпрома. В те времена, челябинские модели не раз были среди лучших на международных конкурсах в Германии, Турции, Польше, постоянно выставлялись на ВДНХ СССР.
10. Резак - это металлическая форма детали с острым краем. Подобно форме для печенья резак кладется на материал и под воздействием тяжести пресса вырезает деталь из кожи. Кстати, на фабрике есть собственное резачное хозяйство, которое изготавливает эти резаки. А в цехах фабрики есть целая «библиотека», где хранится такой резак, для каждой детали, каждой модели, каждого размера.

К концу 80-годов выпуск обуви достиг 12 млн пар в год по всему Челябинскому производственному обувному объединению. Как свидетельствует статистика в 10-й пятилетке (1976-1980) был поставлен план выпустить 62 млн 653 тысяч пар. Кстати, в 1988 году на принципах кооперации с Вьетнамом на фабрике был организован пошив заготовок. Объединение первое в системе Минлегпрома РСФСР заключило прямой договор на изготовление текстильное обуви с предприятием «Сагода».
11. А вот этот агрегат позволяет нанести логотип на стельки.
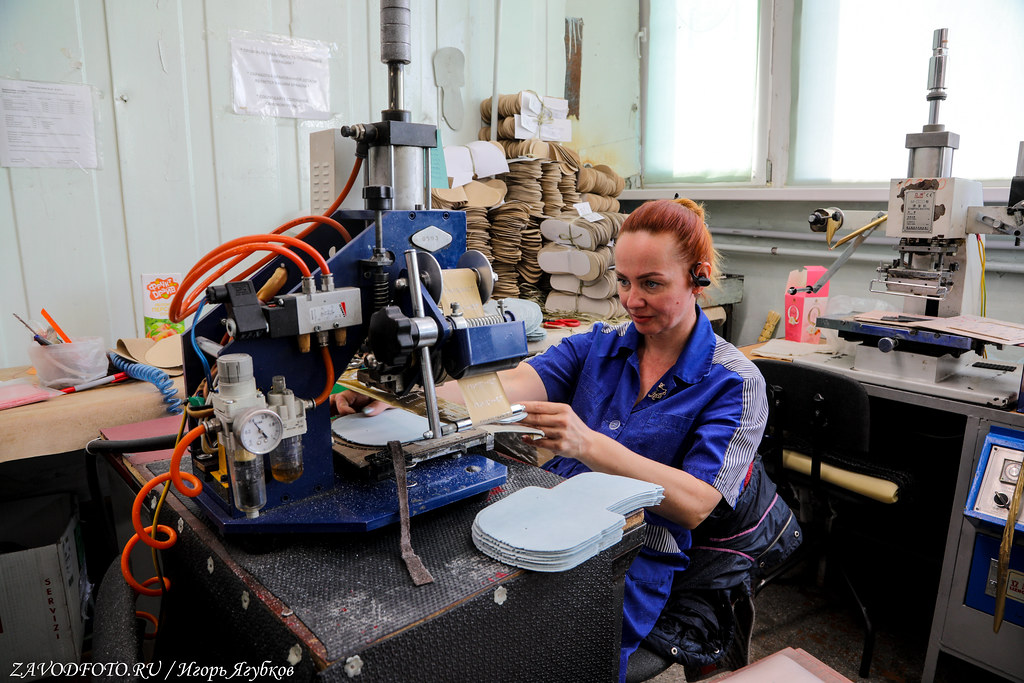
В 1992 году Челябинское обувное объединение было переименовано в «Юничел». От слова union - «союз» (имеется ввиду объединение обувных фабрик Урала, видимо тогда создателям бренда это было важно) и сокращенного названия города Челябинск. Правда, из его состава выведены Златоустовская, Троицкая, Кыштымская обувные фабрики. В этом же году открылся и первый их магазин. Да, в 90-е было нелегко, но выжили, не будем о грустном. С 1999 года под руководством генерального директора Владимира Денисенко началось возрождение производства. В 2001 году фирма выкупила обанкротившееся кожевенно-обувное объединение в Оренбурге, а в 2002 был приобретен контрольный пакет акций обанкротившейся обувной фабрики в Златоусте. В 2016 году челябинская обувная фабрика «Юничел» запустила масштабную программу технического перевооружения предприятия. Закуплено новое оборудование для Челябинской, Оренбургской и Златоустовской фабрик, которые позволили почти в 2 раза увеличить производительность и значительно разнообразить модельный ряд. В ноябре 2016 года компания получила одну из самых престижных премий в российской индустрии моды - «Золотое веретено», за год до этого - Российский Знак качества. Короче, история роста продолжается.
12.
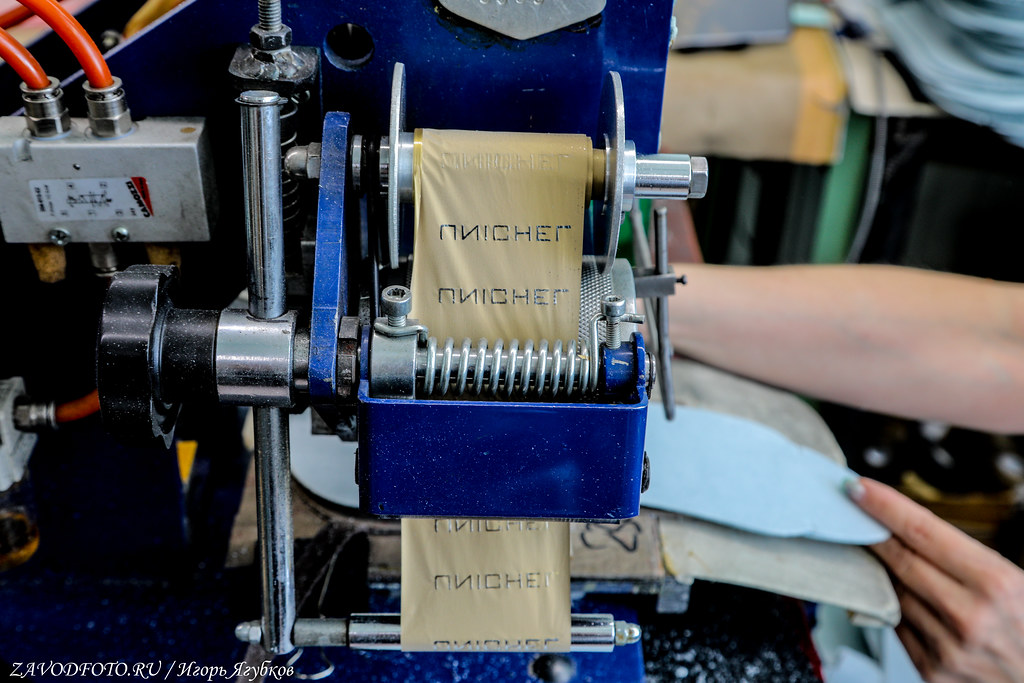
13. Помимо прессов для раскроя кожи есть машины посерьезнее - автоматизированные раскройные комплексы, где на место металлических резаков пришел лазер. Машины быстро сканирует лист кожи, и благодаря своей точности готовы выдавать заготовки даже самых небольших размеров. По сути они выполняют одни и те же задачи, только пресса - это ручной труд, а в новых машинах участие человека, а значит ошибки и неточности, сведены к нулю.

Материал на фабрику «Юничел» поступает в больших рулонах - вес одного может достигать 70 килограммов. Поэтому чтобы раскройщицам было легче работать с такими тяжестями, на помощь им приходит специалист по настилу материалов. Рабочий стол, который он использует, составляет 7 метров в длину. Материал на столе удерживается с помощью специальных держателей - «утюгов», вес каждого из которых 5 кг. Настильщик проверяет материал на наличие брака и укладывает его в настилы слоями от 2 до 20 - в зависимости от толщины материала.
14.

Сегодня «Юничел» - это единственное предприятие на территории Российской Федерации, выпускающее столь широкий ассортимент: мужская, женская, школьная и малодетская обувь для мальчиков и девочек, спортивная и домашняя обувь, модели для отдыха на природе. Обувная фабрика «Юничел» (все три) это 2 500 сотрудников (а если считать занятых в торговле, уже 5 000)! Плюс 630 магазинов в 250 городах России и Казахстана.
15. Кожа сейчас в основном отечественного производства, но и немного Турция помогает.

16. Да, сразу видно - на современное оборудование денег тут не жалеют. А собирали его, видимо, по всему миру, есть китайское, немецкое, итальянское, и этот список можно продолжать. На этом комплексе кроятся промежуточные рулонные материалы: межподклады, поролоны, текстильные материалы, меха. Он позволяет вести раскрой в несколько слоев от 2 до 12 - в зависимости от материала.

17. На таких станках тут тоже кроят промежуточные материалы: основные стельки, подноски, задники - картоны разной толщины и плотности.

18.
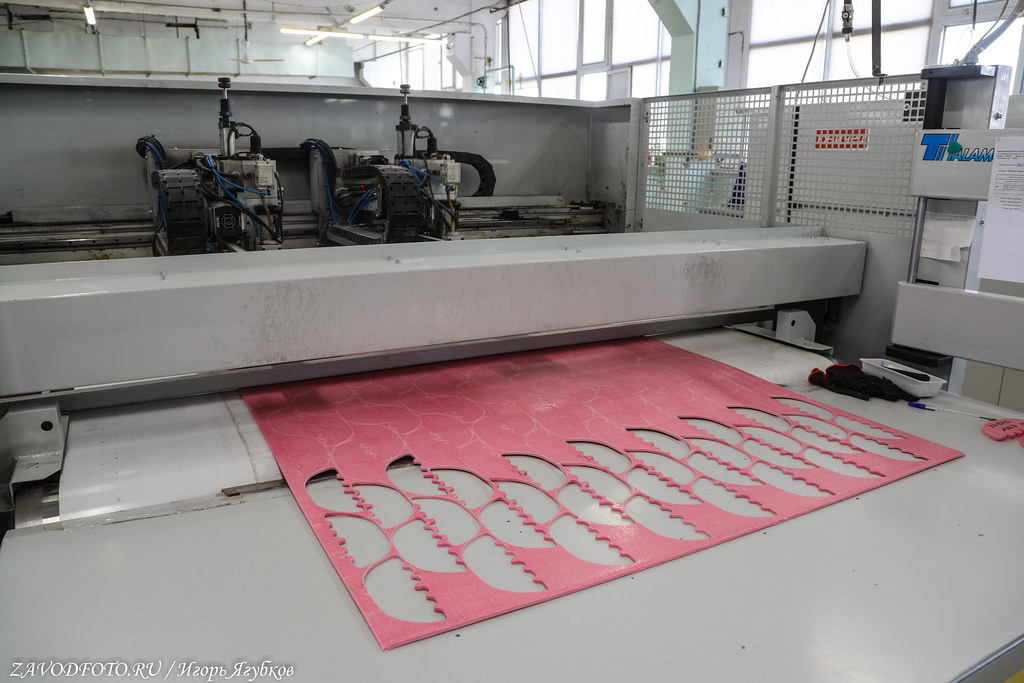
19.

Фабрика настолько большая, при этом сразу на нескольких потоках собирается разная обувь, что проследить за одной моделью весьма проблематично. Поэтому предлагаю сразу вкратце рассказать весь технологический процесс. После того, как дизайнеры и модельеры придумали ту или иную модель, подобрали нужные материалы, настаёт очередь производства. Далее, на первом этапе происходит вырезка заготовок, это делается с помощью гидравлических прессов или более сложных комплексов, где оператор выбрав нужный расклад лишь контролируют процесс. Полностью готовые к сборке детали поступают в следующий цех, где из них начинают собирать уже верх обуви. Операции разбиты на этапы, по сути, это конвейер, где каждый выполняет ограниченное количество операций, хотя простыми некоторые из них назвать очень сложно. Таким образом, постепенно рождается почти готовое изделие, правда, ему не хватает для счастья подошвы. Спокойно, не расходимся, в других цехах она тоже уже готовится.
20. Швейный цех.

21.

22. Рабочий день на фабрике длится восемь часов, с пол восьмого до четырех (понятно минус обед, пятиминутки). Как мы видим, балом правит тут, в основном, прекрасный пол, а им и деткам надо внимание вечером уделить, да и мужей голодными не оставить :).

23.

Верх обуви, который собирают в этом цеху, изготавливается отдельно от подошвы и включает в себя следующие детали: Переднюю часть изделия - носок; Среднюю часть изделия - союзку; Часть, фиксирующую верх ноги - язычок; Заднюю часть изделия, фиксирующую пятку - задник. Да, можно ещё углубиться, вспомнить про Берцы - наружная деталь верха обуви, закрывающая тыльную поверхность пяточно-геленочной части стопы, иногда в части голени.

24.

25.

26. Чтобы собрать одну пару обуви в среднем нужно проделать порядка 80 различных технологических операций.

27.

28.

29.

30.

31.
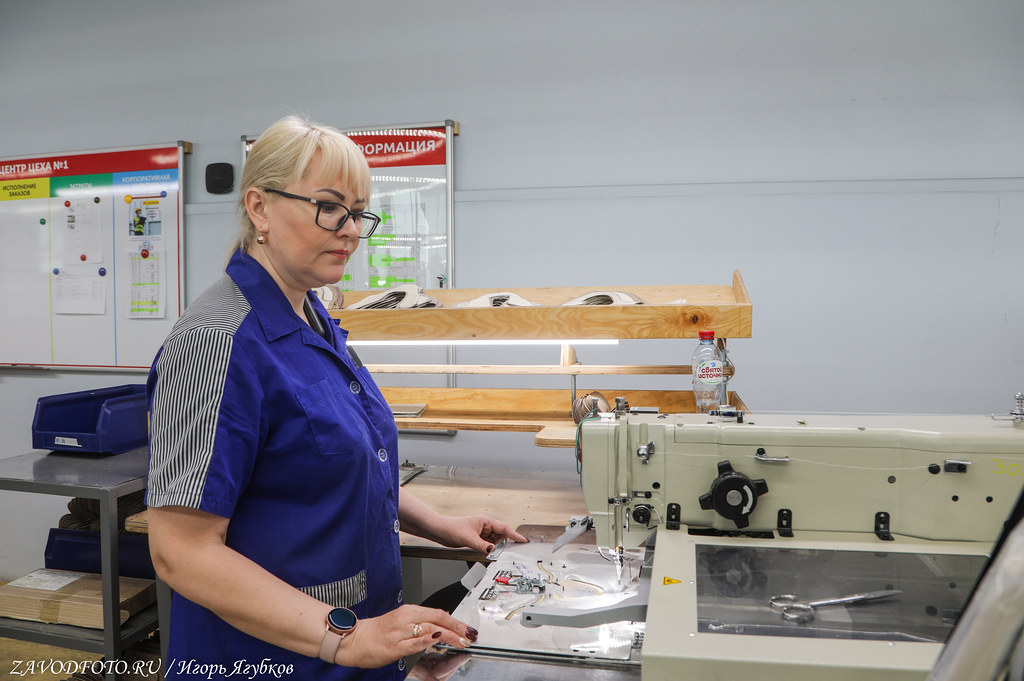
32. Два из трёх миллионов производимых на фабрике пар обуви создаются на основе подошвы собственного производства. Её изготовление ведется на литьевом участке.

33. На этом участке заливают полиуретан в формы для подошв.

34. Тут же происходит и свадьба верха кроссовка с подошвой.
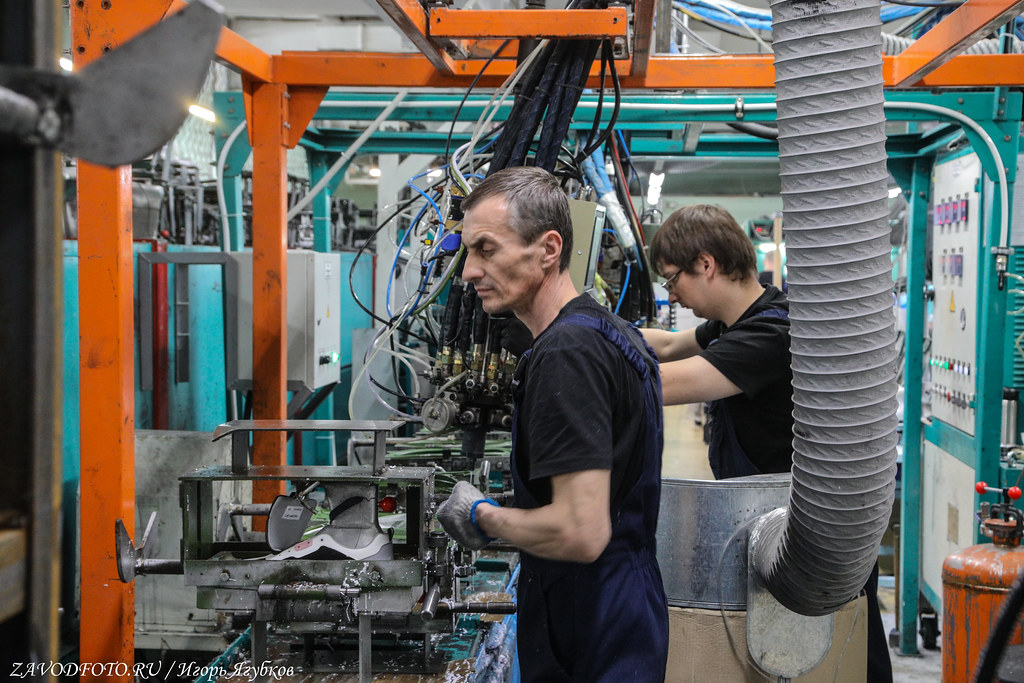
35.

36. В мировой обувной промышленности изготовлением подошв, как правило, занимаются специализированные предприятия. Но в нашем случае опять всё "сами с усами".
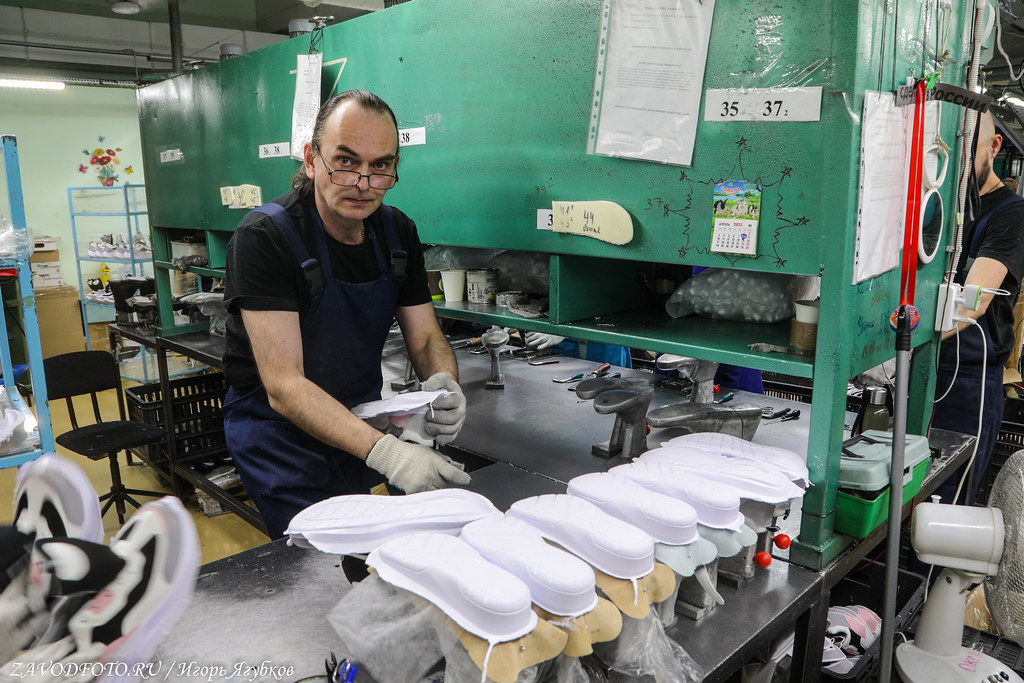
37. Инфракрасная печь как раз и помогает сделать эту связь крепче.

38. Металлические ноги для литьевых машин.

39.

40.
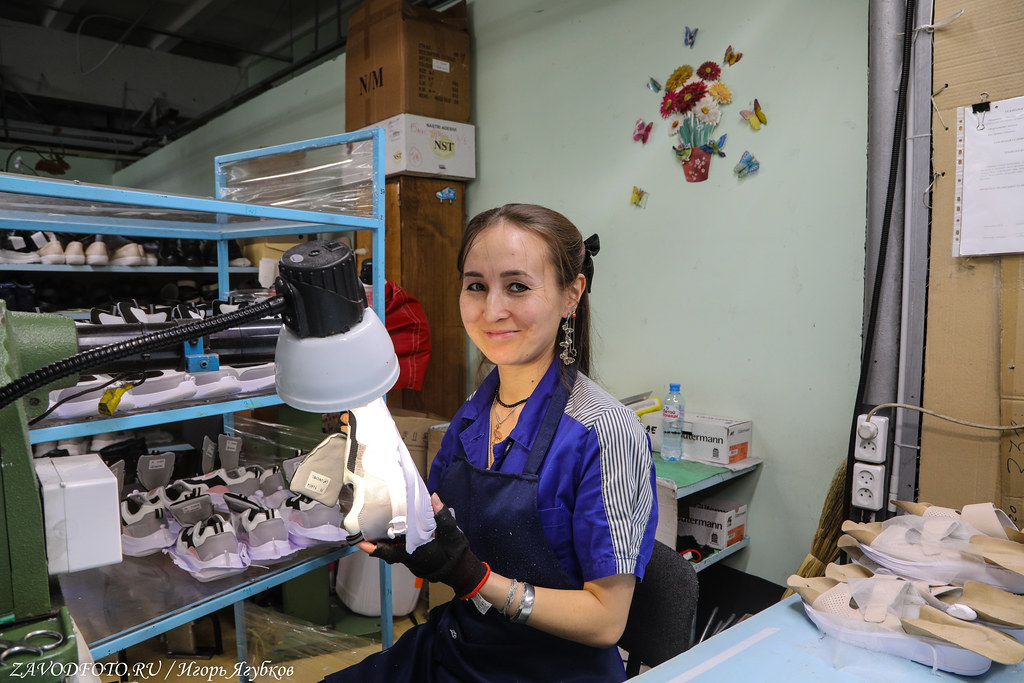
41. Участок по сборке детской обуви.

42.
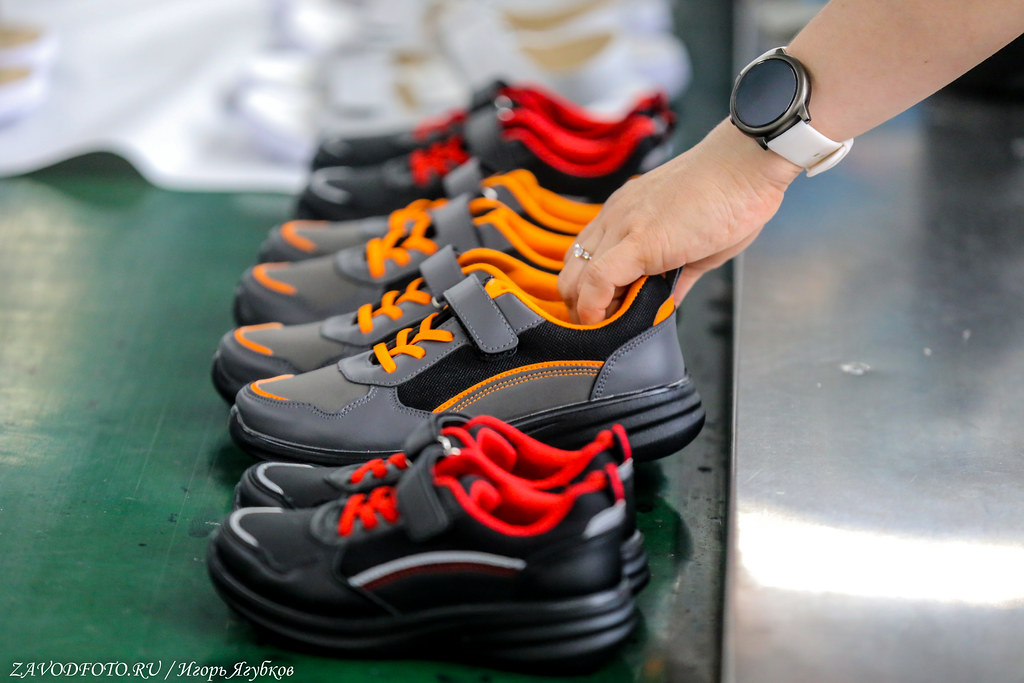
43.

44.
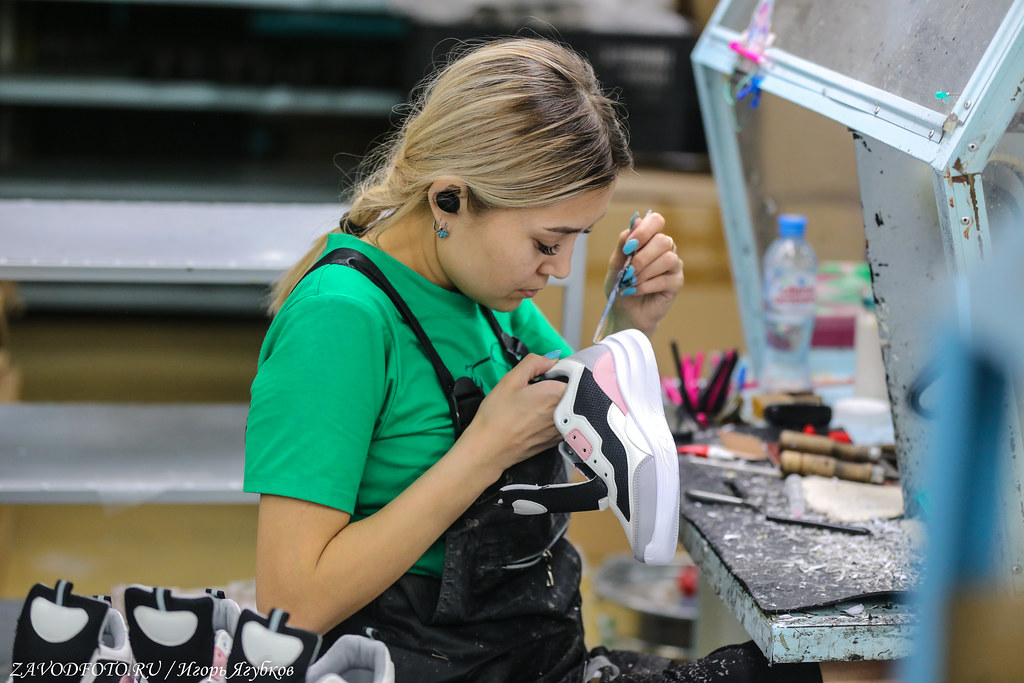
45. Эта умная машина отвечает за шнурки.

46. А знаете, как называются пластиковые или металлические наконечники на шнурках? Эглеты! На фабрике стоит специальная машина для установки эглетов. При этом длину шнурков можно задать любую, в зависимости от модели и размера обуви. Шнуруют всю обувь вручную. На полупаре может быть от 8 до 36 отверстий для шнурков в зависимости от модели.

47. Ещё один участок, где делают подошвы, которые потом приклеивают или пришивают к обуви.
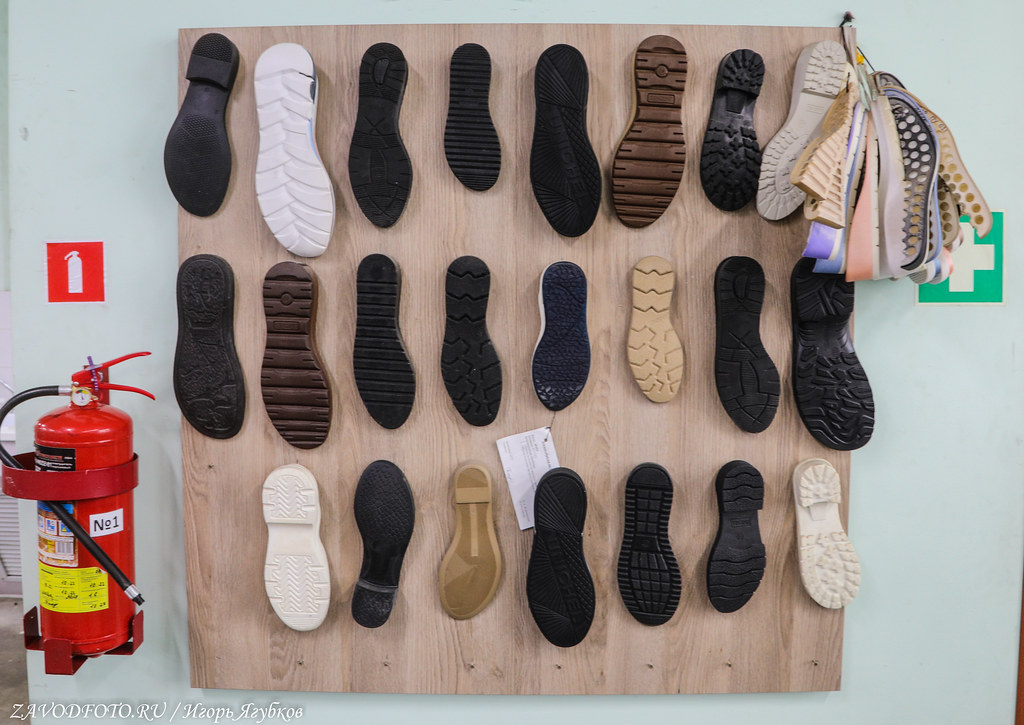
48.
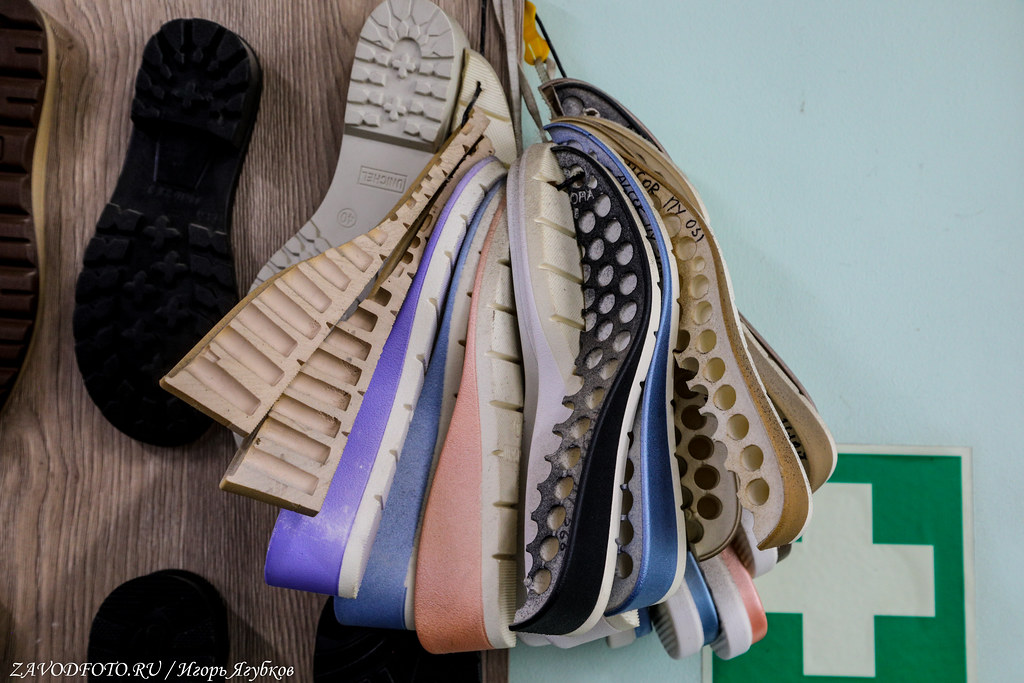
Конвейер с формами для заливки полиуретана. С одной его стороны в воронку засыпаются специальные гранулы из полимерного материала - пластикат. Внутри агрегата происходит его вулканизация и разогрев, полученная мягкая масса выливается через сопла в пресс-формы. Форма смыкается, проходит один круг через вентилятор и в результате получают готовую подошву. Модели подошвы могут быть любой сложности. При необходимости подошва окрашивается, вручную, или в специальной матрице с захлопывающейся крышкой, которая позволяет покрасить не всю подошву, а только ее часть. Подошва может быть двухцветной, тогда она проходит два круга: сначала один круг с пластикатом одного цвета. Потом в те же пресс-формы заливается уже второй цвет.
49.

50.

51.
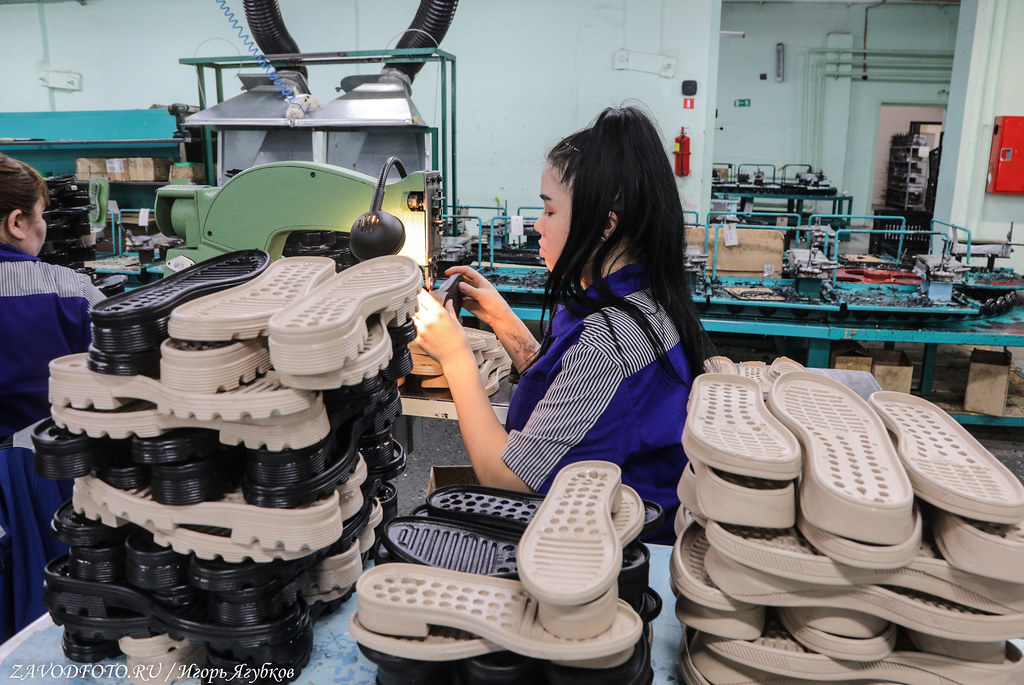
52.
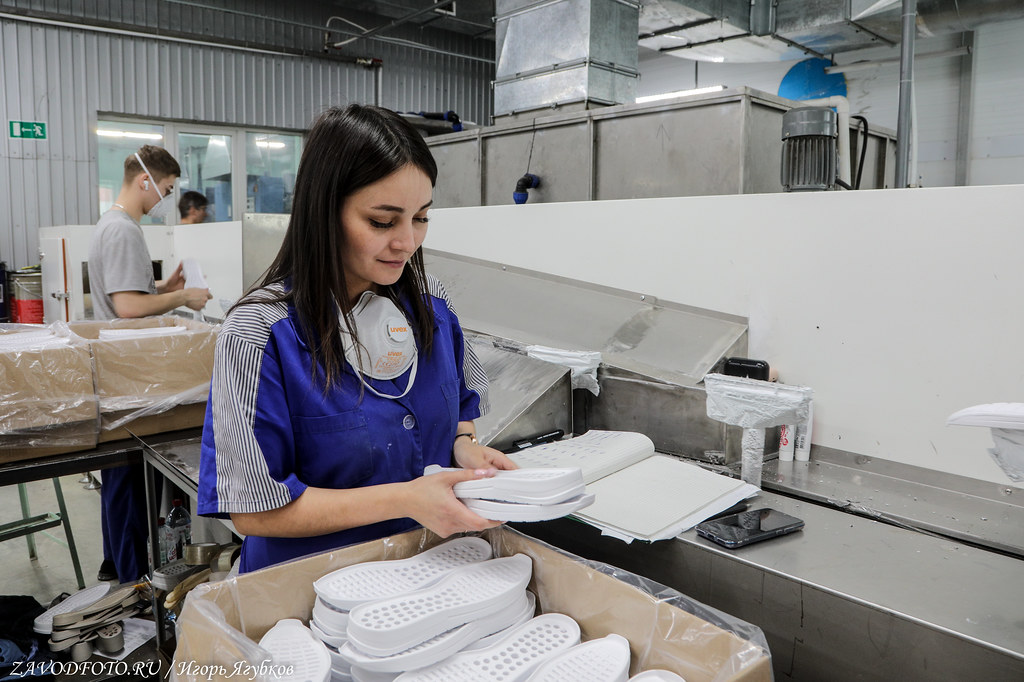
53. Всё лишнее тут же обрезается.

54.

55. «Обувная карусель» для смягчения краев обуви.

56.

57. На этом агрегате происходит придавливание верха ботинка к колодке. Также обжимается нижняя часть, чтобы на следующем этапе успешно подклеить стельки и подошву.
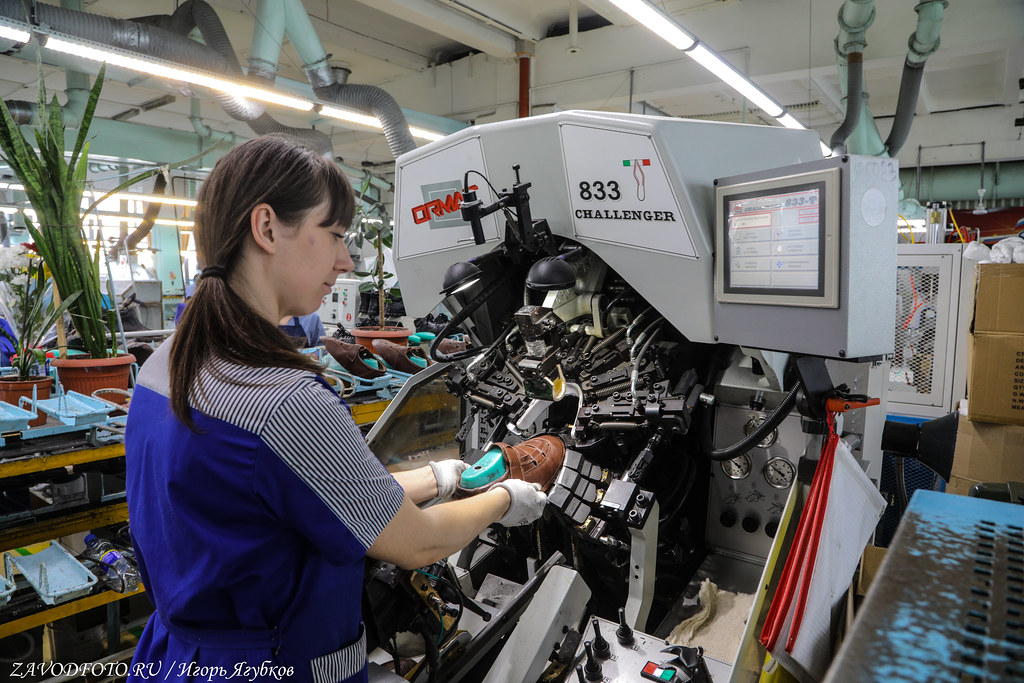
Затяжка. Суть этого процесса состоит в том, чтобы придать плоским деталям верха обуви пространственную форму: чтобы носок был острым, а пятка округлой. Желаемая форма задается размерами и формой затяжной колодки. Затяжка пяточно-геленочной части. Данный этап начинается с предварительного формования пяточной части. В заготовку устанавливается задник, а затем, чтобы пятка приняла нужную округлую форму без складок, идет формование: в момент нагревания придается нужная форма, а момент охлаждения закрепляет ее. Затяжка носочно-пучковой части. Здесь то же самое оборудование, только затяжка носочной части.
58.
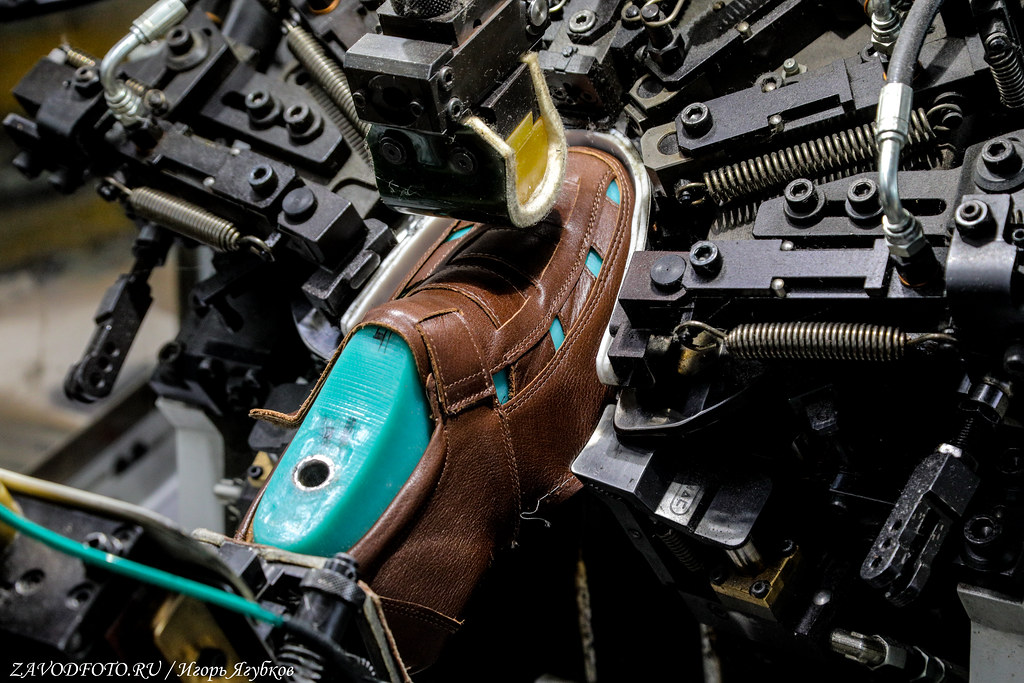
59. Одна машина затягивает минимум 450 пар обуви в день.

60.
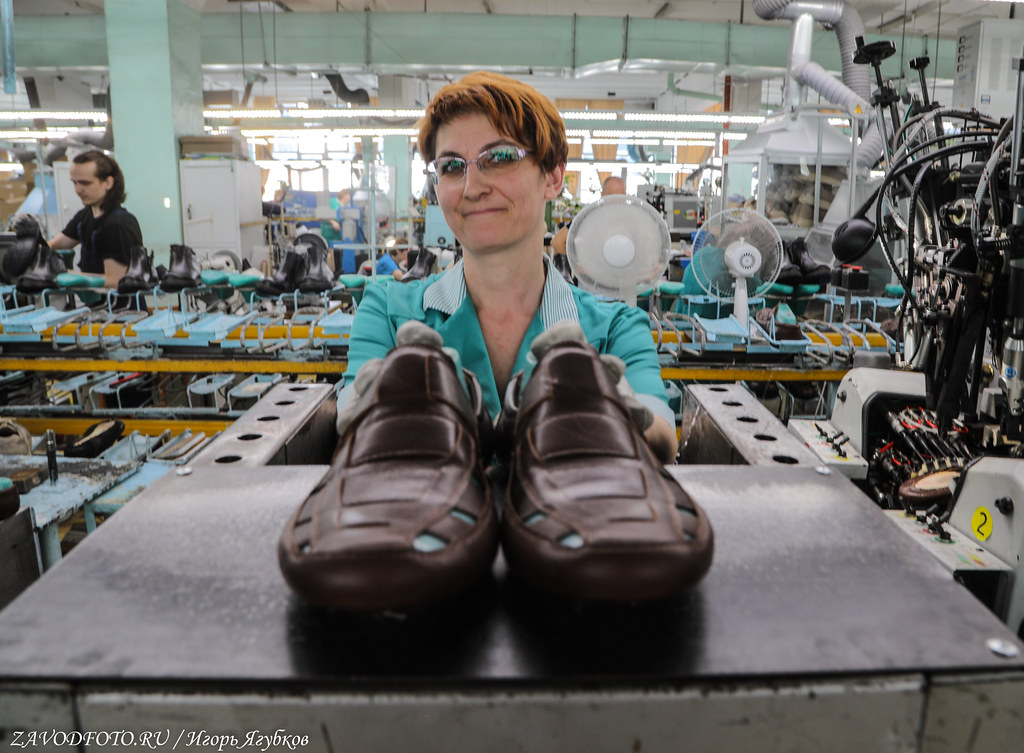
61.

62.
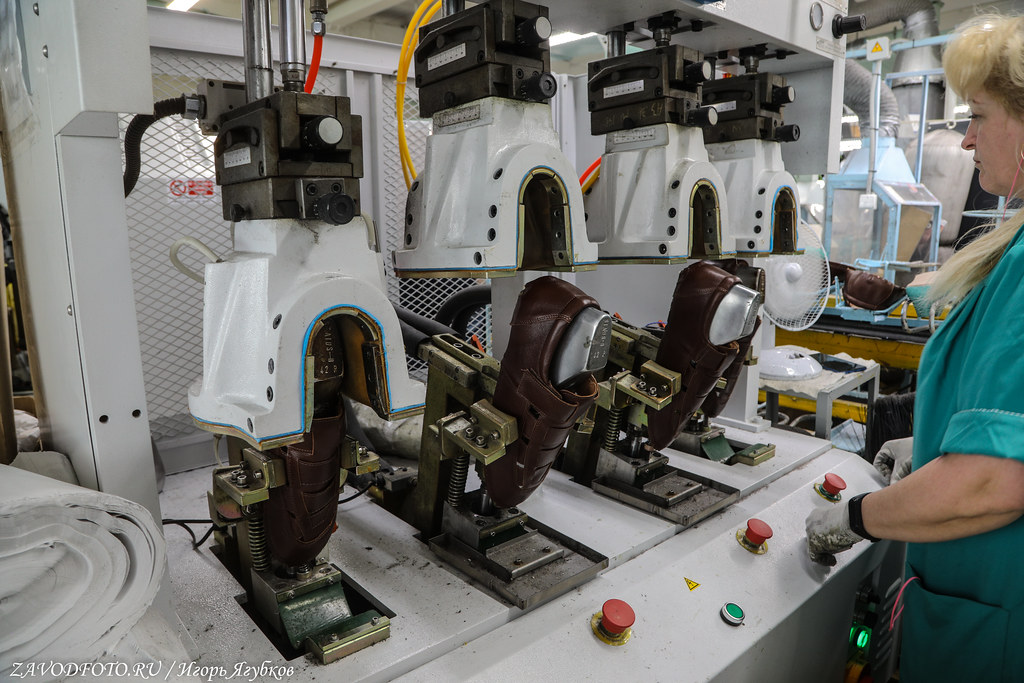
63.

64.

65. Колодки они тоже умеют делать сами. Между прочим, далеко не каждое наше предприятие может похвастаться таким умением. Давайте и туда заглянем, раз нам везде дали зелёный цвет.

66. Собственный колодочный цех для Юничел даёт ряд преимуществ. Во-первых, это возможность сократить затраты, а значит снизить себестоимость обуви. Во-вторых, возможность для максимального усовершенствования колодки. В результате обувь получается дешевле, не в ущерб качеству. Разве это не здорово, тем более в наше время.
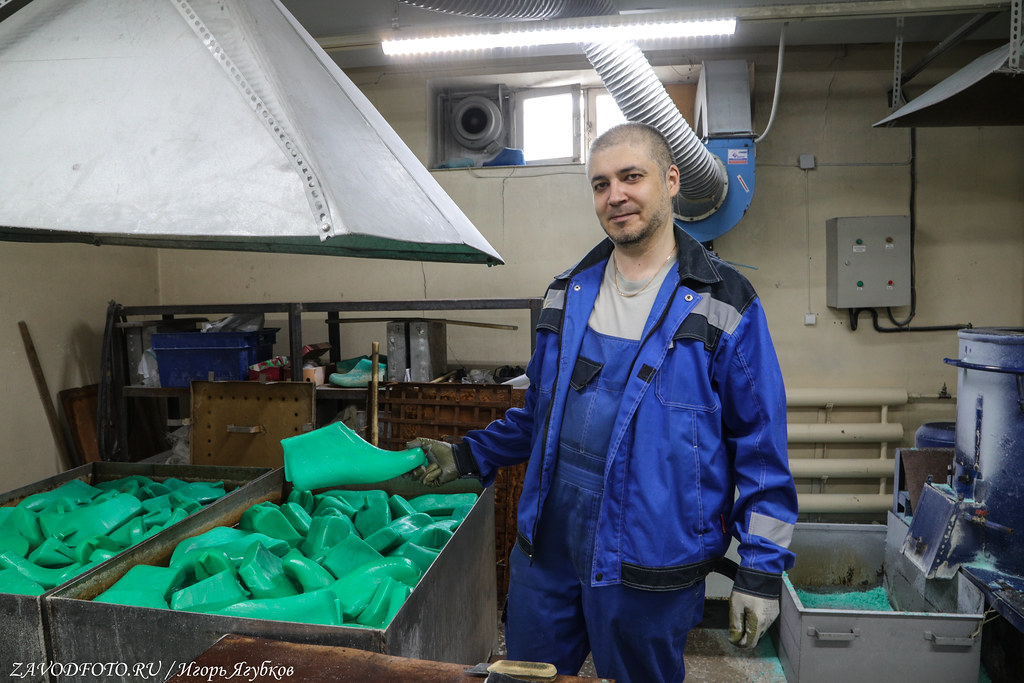
67. Всё волшебство происходит на этом оборудовании. Сюда приходит сырьё его загружают в экструдер и вуаля. Правда пока получился лишь черновой вариант, его ещё нужно обработать.

68. Каждая колодка желает внимания руки мастера.

69. Кстати, именно от колодки начинается дизайн будущей обуви. Ведь вся соль, как раз в геометрии будущей обуви. Насколько она будет удобна, плюс колодка содержит в себе информацию о высоте каблука, ширине и форме носка. Представляете, чтобы оправдать трудозатраты на изготовление одной колодки, дизайнер должен создать на ее основе не менее пяти разных моделей.

70. Из серии "интересный факт". Оказывается, колодки для нас отличаются от аналогичных для итальянцев или китайцев. У нас стопа при прочих равных шире и имеет более крутой подъем. А ещё и в регионах свои особенности. Например, в Ижевске, Чите и Улан-Удэ чаще можно встретить покупателей с маленькой стопой, поэтому туда обувщики больше отправляют обувь с маленькими размерами, а в Новосибирске и Оренбурге чаще спрашивают большие размеры, чем в среднем по стране.
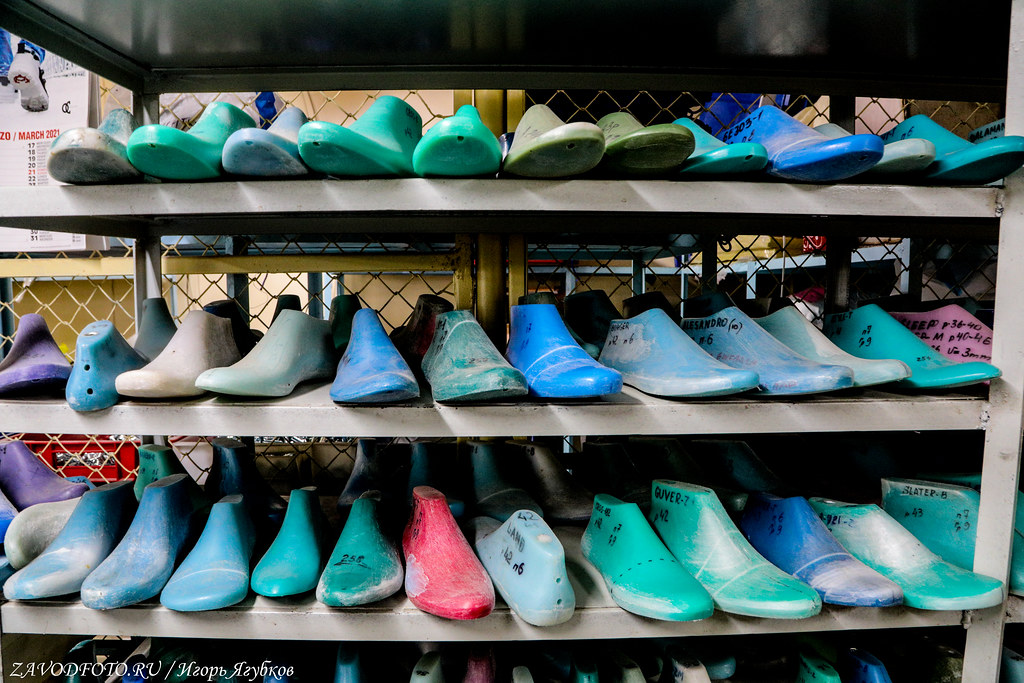
71. Ой, чья туфля? Кстати, туфли-лодочки, как говорят сами обувщики - самая сложная в производстве обувь.

72.

73.

Чтобы нанести на обувь различные рисунки необходима тампография. Это когда в специальное оборудование заливается краска, на матрице выбирается рисунок или надпись. Силиконовая подушка опускается на матрицу, рисунок отпечатывается на подушке, и потом эта подушка окрашивает часть верха или сам каблук. Окрашиваются и голенища, это происходит по такому же принципу. С помощью тампографии можно нанести на обувь бесконечное количество цветов и оттенков различных рисунков.
74.

75.

76. Вся работа по сборке обуви на фабрике организована в виде конвейера. Причем существует конвейер как принудительного вида, так и свободного. На фото - принудительный конвейер: он не дает расслабляться и отвлекаться, так как двигается с фиксированной скоростью.

77.

78.

79.

Участок намазки кремом - финишная отделка. Чтобы обувь была более красивая, яркая, законченная она обрабатывается кремом и полируется. Процедура проводится дважды: после первого раза крем впитывается, полировкой забивается в поры, а затем наносится еще один финишный слой для того, чтобы поверхность блестела. Крем используется на водной основе с воском, чтобы вода не пропиталась в обувь. И, наконец, последний штрих - полировочный воск, который придаёт блеск обуви.
80.
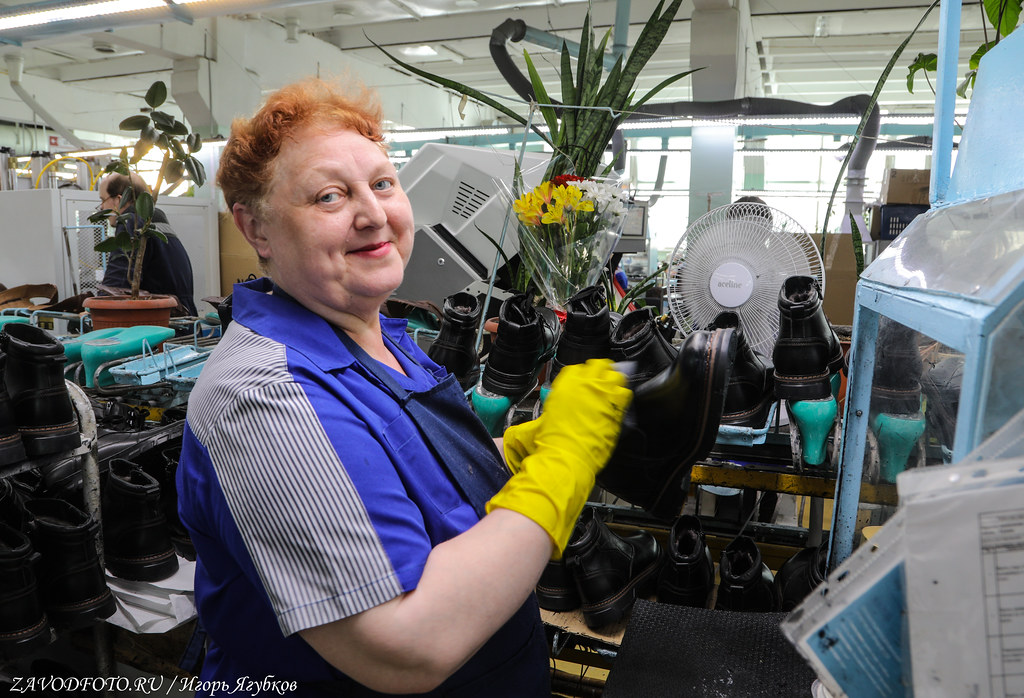
81. Юничел особенно любит работать с кожаной обувью, ещё раз напомню, 10% всей произведенной кожаной обуви в стране - это их заслуга!

В России в среднем производится 100 миллионов пар обуви в год, из них 20 миллионов - кожаной. При этом продается в пять раз больше. 80 % от этих 500 миллионов завозятся, и в основном - из Китая. А треть всей ввозимой обуви ввозится в страну вообще нелегально.
82.

Понятное дело, что на таком серьёзном производстве про контроль, конечно же, не забывают. Ведь «Юничел» - это фабрика по производству идеальной обуви. Кроме визуального осмотра, каждая модель проходит тест на отрыв подошвы. Если подошва отходит, тогда корректируют параметры клея: изменяют температуру при наклеивании, поправляют химический состав. Есть тут и своя лаборатория, правда, в этот раз мы про неё забыли и не зашли на огонёк, но есть повод вернуться :).
83.

84. Ну вот, собственно, и финиш. Готовая пара укладывается в коробку, упаковывается, получает гарантийный талон и отправляется на склад готовой продукции, а дальше в магазины и навстречу новому хозяину. Кстати, и коробки тут тоже сами собирают. Каждый сборщик бумажных изделий за смену собирает 1500 и больше коробок!

В бизнесе есть простая истина - мало что-то произвести, главное потом это продать. На Юничеле это поняли почти сразу и стали развивать торговую сеть. Тем более, что бонусом этой истории как раз прямая связь с клиентом, что ему нравится, а где надо ещё приложить усилия, чтоб его удивить. Сегодня уже более 630 магазинов в 250 городах России и Казахстана работают под брендом «Юничел».
85.
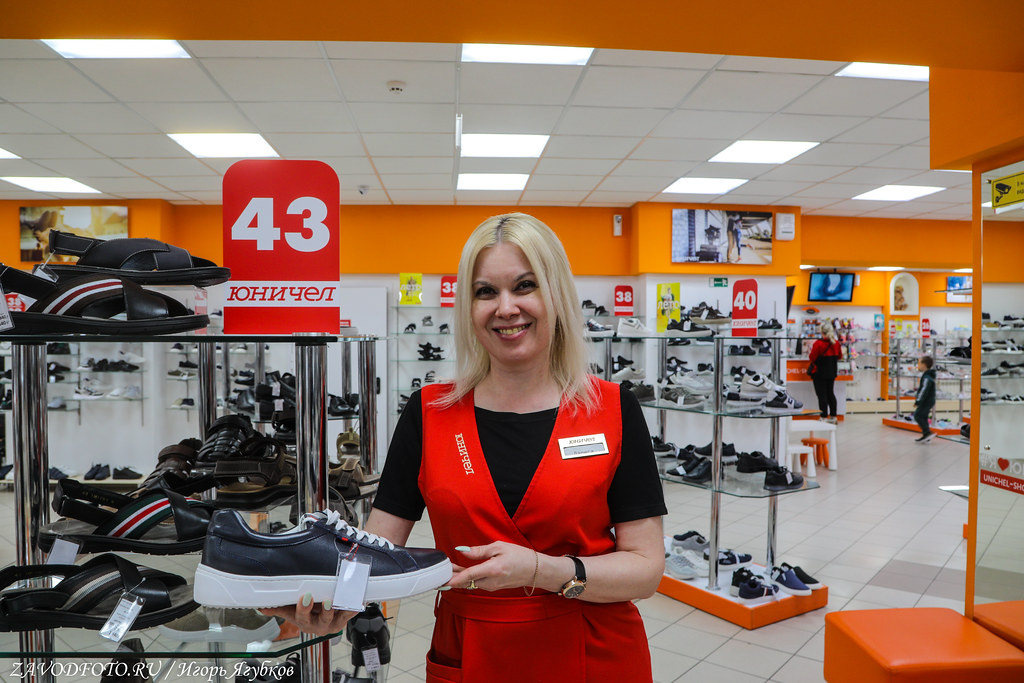
Я уже признавался, что до этой поездки я про Юничел, конечно, слышал, а вот в их магазинах так и не был. Так вот прямо при фабрике у них есть большой магазин, конечно же, я не мог в него не зайти, тем более, что меня пряником поманили, сказали, если что-то понравится, мы можем и подарить :). Признаюсь, ушёл не с пустыми руками, выбрал вот такие синенькие, как вам? Уже неделю хожу, весьма удобные, легкие, и не мозолят, так что на следующем производстве точно буду в них.
Кстати, чтобы посмотреть модели и цены можно просто посетить интернет-магазин:
https://unichel-shop.ru/23 А для моих читателей до 28 мая действует дополнительная скидка в онлайн-магазине по персональному промокоду: UNIDAY
86.

87.
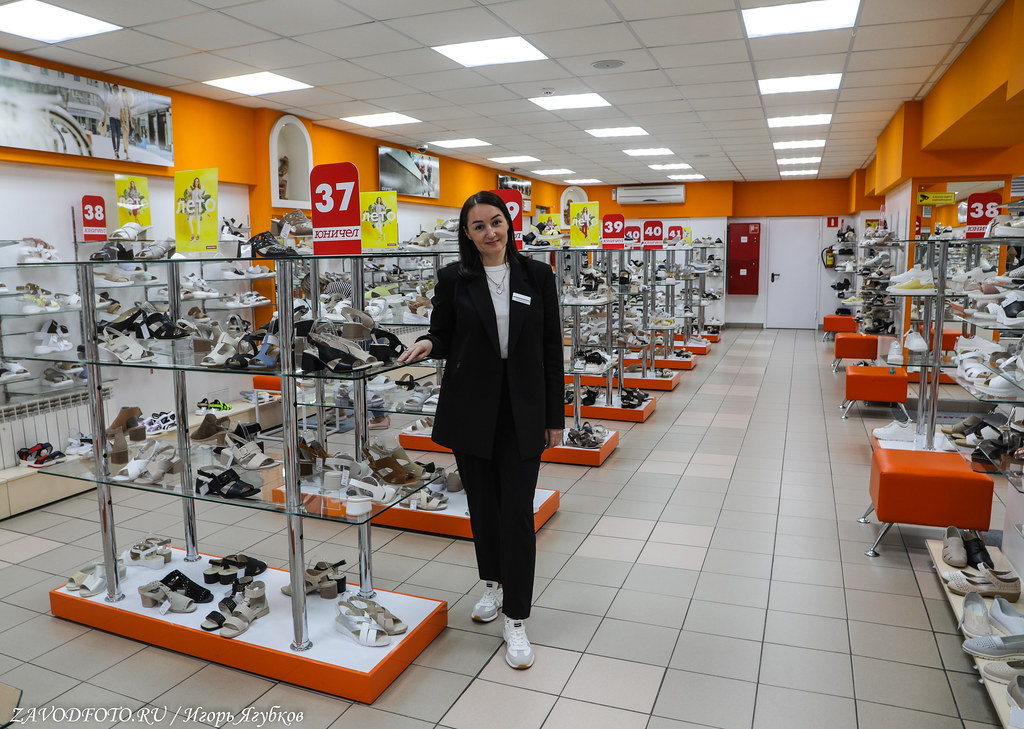
88.

89. А цены-то реально весьма демократичные.

90.

В качестве резюме добавлю - Юничел реально нужно уважать. Ведь именно такие компании и создают по-новому индустрию моды в нашей стране, особенно когда буржуи сбежали, как крысы с корабля. Они делают качественную обувь по разумной цене, и всё для этого у них есть: первоклассное оборудование, надежные поставщики, большой опыт.
Также за жизнью и новинками бренда можно следить здесь:
Вк @unichelИнста @unichel_shoes
91.

92. Знакомьтесь, Владимир Денисенко - основатель и генеральный директор фирмы «Юничел». Очень здорово, когда ты приезжаешь на предприятие, а тебя ещё и первое лицо встречает. Тем более с таким опытом, ведь вся его трудовая деятельность, в основном, связана именно с лёгкой промышленностью. После окончания Новосибирского института легкой промышленности он сначала работал главным механиком на Кыштымской обувной фабрике, потом был директором Троицкой обувной фабрики. Затем учил уму разуму во Вьетнаме местных обувщиков, в шутку признается - на свою голову :). И, наконец, прошёл путь от главного инженера Челябинской фабрики, до генерального директора. Короче, настоящий профессионал, который любит свое дело. Большое спасибо всем сотрудникам компании «Юничел» за открытость и тёплый приём!
