Ко Дню Космонавтики немного космического железа вам в ленту.
И так, в экспозиции Музея изобретателя электросварки Н.Г.Славянова, в зале современные способы сварки, находятся четыре предмета имеющие отношение к ракетному двигателю РД-276 РН "Протон-М".
«Прото́н» (УР-500 - Универсальная ракета, «Протон-К», «Протон-М») - одноразовая ракета-носитель (РН) тяжёлого класса, предназначенная для выведения автоматических космических аппаратов на орбиту Земли и далее в космическое пространство. Cпособна выводить на геостационарную орбиту (ГСО) грузы до 3,3 т. Разработана в 1961-1967 годах в подразделении ОКБ-23 (ныне ГКНПЦ им. М. В. Хруничева).
РН «Протон» явилась средством выведения всех советских и российских орбитальных станций «Салют-ДОС» и «Алмаз», модулей станций «Мир» и МКС, планировавшихся пилотируемых космических кораблей ТКС и Л-1/«Зонд» (советской лунно-облётной программы), а также тяжёлых ИСЗ различного назначения и межпланетных станций.
С середины 2000-х годов основной модификацией ракеты-носителя «Протон» стала РН «Протон-М», используемая для запуска как федеральных российских, так и коммерческих иностранных космических аппаратов.
История создания
В 1961 г. - начаты проектные работы по двигателю РД-253 на компонентах НДМГ-АТ для лунной ракеты Н1. Двигатели РД-253 после доработки решено применить в составе ДУ первой ступени ракеты УР-500.
16 июня 1965 г. - первый пуск двухступенчатой УР-500 (8К82).
1987 г. - начало разработки форсированного двигателя РД-275 для РН «Протон»
В октябре 1995 г. - первый пуск РН «Протон» с двигателями РД-275 (14Д14)
2001 г. - начало разработки форсированного на 5.2% по тяге двигателя РД-275М (14Д14М, в документах ОАО "Протон-ПМ" - РД-276).
14 апреля - 15 июня 2005 г. - двигатель РД-275М (14Д14М) успешно прошел программу межведомственных испытаний. Началось серийное производство новой модификации двигателя.
7 июля 2007 г. - первый пуск РН «Протон-М» с двигателями РД-275М (14Д14М)
Общие сведения
Двигатель выполнен по замкнутой схеме с дожиганием окислительного генераторного газа после турбины.
Компоненты топлива: окислитель - четырехокись азота (азотный тетраоксид, AT), горючее - несимметричный диметилгидразин (НДМГ).
Двигатель содержит камеру сгорания, турбонасосный агрегат (ТНА) с турбиной и насосами окисоителя и горючего, газогенератор, струйный преднасос окислителя, генераторфы газа для наддува топливных баков, агрегаты автоматики и другие элементы.
Управляющие моменты создаются качанием всего двигателя в шарнирном подвесе. Т.к. качание происходит в одной плоскости, в многодвигательной ДУ двигатели установлены с угловым смещением относительно друг друга.
Давайте теперь рассмотрим наши артефакты.
Перед нами магистраль подвода окислителя М013-100В жидкостного ракетного двигателя РД-276. Изготовлена в 2012 г.
Является цельносварным узлом, подающим тетраоксид азота из бака к насосу окислителя при запуске РД-276 ракеты-носителя «Протон».
Использованные материалы: хромоникелевый сплав 09Х16Н4Б, нержавеющая сталь 12Х21Н5Т
Способ изготовления: ручная аргонодуговая сварка, автоматическая, дуговая сварка в среде защитных газов.
Что мне показалось любопытным в этом изделии? Во-превых поразила скорость истечения окислителя по этому трубопроводу. Что-то типа 200 литров в секунду, но я могу ошибаться. В результате такой скорости на трубопровод действуют колосальные нагрузки и чтобы бороться с ними нужны определенные прочностные характеристики изделия. Второй момент: при прохождении окислителя с такой скоростью по трубопроводу возникают всевозможные вибрации и кавитация. Чтобы избежать этого в окислитель уже на стадии прохождения трубопровода подается горючее (?).
На нашем изделии разрез произведен по струйному преднасосу окислителя, а точнее по его сопловому аппарату
Рис. 2. Струйный преднасос окислителя
1 - сопловой аппарат
2 - конфузор
3 - смесительная камера
4 - диффузор
Струйный преднасос создает дополнительный напор (0.17 МПа) на входе в насос окислителя, что обеспечивает бескавитационную работу насоса при достаточно низком давлении в баке. Представляет собой сварную конструкцию и состоит из соплового аппарата, конфузора 2, смесительной камеры 3 и диффузора 4. Окислитель под высоким давлением подводится в коллектор соплового аппарата. Из коллектора через отверстия в кольце активный поток направляется в конфузор и смесительную камеру 3, где, смешиваясь с основным потоком компонента, сообщает дополнительную скорость основному потоку. В диффузоре 4 скоростной напор потока преобразуется в статическое давление. Но эта часть у нас отрезана.
На этом фото можно хорошо разглядеть сопловый аппарат
В нижней части стоящей вверх ногами магистрали подвода окислителя расположен компенсатор для обеспечения гибкости соединения магистрали окислителя.
Устройство компенсатора
1 - кольцо
2 - кольцо
3 - сильфон
4 - штуцер
5 - фланец
6 - кронштейн
7 - кронштейн
Компенсатор обеспечивает возможность качания изделия на угол ±8. Гибкой частью компенсатора является сильфон 3, приваренный к кольцу 1 и фланцу 5. Между гофрами сильфона расположены резиновые кольца 2 для сохранения профиля гофра при наличии давления внутри сильфона и изгиба компенсатора при качании изделия.
Вид с другого ракурса
Камера сгорания РД-276
Рис. 3. Камера сгорания
1 - смесительная головка
2 - кольцо соединительное
3 - камера сгорания
4 - кронштейн
5, 6 - штуцера
7 - кронштейн
8 - реперная площадка
9 - сопло
Камера сгорания представляет собой паянно-сварную конструкцию, состоящую из смесительной головки, цилиндрической части камеры и профилированною сопла, закритическая часть которого выполнена с угловым входом. Соединение деталей и узлов КС осуществлено путем сварки и пайки твердым припоем.
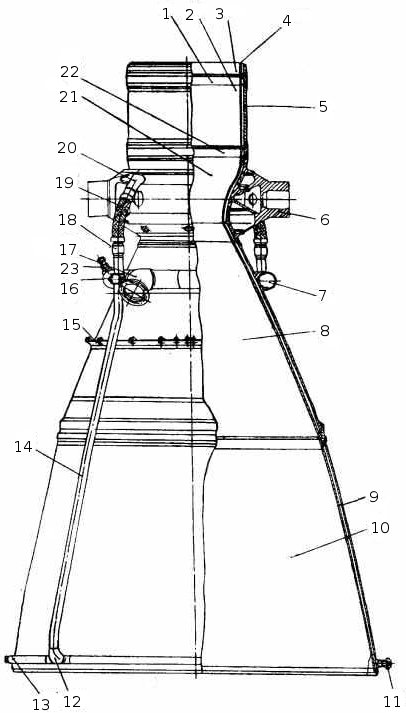
Рис.4. Конструкция камеры сгорания
1 - верхний пояс завесы
2 - 2-я (нижняя) цилиндрическая секция камеры сгорания
3 - 1-я (верхняя) цилиндрическая секция камеры сгорания
4 - огневая стенка
5 - внешняя оболочка камеры
6 - бандаж с цапфами
7 - коллектор
8 - 1-я секция сопла
9 - проставка гофрированная
10 - 2-я секция сопла
11 - штуцер
12 - угольник
13 - коллектор
14 - трубопровод
15 - перегородка
16 - кронштейн
17 - угольник
18 - переходник
19 - трубопровод
20 - угольник
21 - средняя часть камеры
22 - нижний пояс завесы
23 - штуцер
Камера сгорания (КС), включающая цилиндрический участок камеры, докритическую и закритическую части сопла, состоит из следующих основных узлов: двух секций цилиндра 3 и 2; двух поясов завесы 1 и 22; средней части 21; первой секции сопла 8; сопла-надставки 10.
Каждый из основных узлов состоит из внутренней стенки и наружной рубашки. Внутренние стенки цилиндра, завесы, средней части и первой секции сопла соединяются между собой сваркой, а рубашки свариваются при помощи соединительных колец.
Наружные рубашки с внутренними стенками секций цилиндра, поясов завесы, средней части и первой секции сопла спаяны по вершинам ребер, выфрезерованных на наружной поверхности стенок. Образованные ребрами каналы служат для протока охлаждающей жидкости.
На внутренней стенке каждого пояса завесы имеется кольцевая канавка, сообщающаяся при помощи тангенциальных отверстий (сечение по АА) с зарубашечным пространством.
К рубашке средней части 21 приварен бандаж с цапфами 6.
На первой секции сопла 8 находится коллектор 7 с патрубком 17 (угольником) для ввода горючего. Для прохода "Г" из коллектора в зарубашечное пространство в рубашке просверлены отверстия. От штуцера 23 производится отбор горючего к газогенератору наддува.
На перегородке 15, припаянной к рубашке, крепится защита двигателя. Для крепления ТНА приварен кронштейн 4.
Стенка и рубашка сопла-надставки 10 соединены между собой пайкой через гофрированные проставки 9.
Коллектор 13 с патрубками 12 (угольниками) служит для отвода охладителя из зарубашеченное пространства сопла-надставки. На коллекторе имеется штуцер 11 для слива горючего.
Перепуск горючего из коллектора 13 в коллектор бандажа 6 производится по четырем трубопроводам 14, приваренным к угольникам 12 и 20. Температурная компенсация длины трубопроводов обеспечивается гибкими шлангами 19.
Внутренние стенки цилиндра, завесы, средней части и первой секции сопла изготовлены из специальной бронзы. Наружная рубашка, коллекторы и бандаж с цапфами выполнены из нержавеющей стали повышенной прочности.
На внутренние поверхности стенок, кроме щелей завесы и сопла-надставки, нанесено циркониевое покрытие.
Окислитель поступает в форсуночную головку из ГГ в виде окислительного газа, горючее подводится к коллектору 7, откуда проходит по зарубашечному тракту КС и поступает в ФГ с некоторым запаздыванием относительно окислителя. Из полостей окислителя и горючего ФГ компоненты топлива через форсунки впрыскиваются в цилиндрическую часть камеры, где протекает процесс сгорания распыленного топлива. В сопле происходит расширение газа, сопровождающееся уменьшением его давления, температуры и увеличением скорости истечения.
Вот так выглядит фрагмент цилиндра камеры сгорания жидкосного ракетного двигателя РД-276. Деталь изготовлена в 2007 г. и представляет собой паяно-сварную конструкцию корпуса камеры сгорания 1-ой ступени РД-276 ракеты-носителя «Протон».
Использованные материалы: хромоникелевый сплав 09Х16Н4Б, бронза БрХ08
Технология изготовления: высокотемпературная пайка под давлением в вакуумно-компрессионном агрегате, электронно-лучевая сварка в вакууме, автоматическая сварка в среде защитных газов.
На фото хорошо видна сотовая структура стенок КС, щели завесы и циркониевое порошкообразное покрытие внутренних стенок камеры. Узел на фото перевернут вверх ногами и мы видим камеру сгорания как будто бы засунув в нее голову снизу. При таком ракурсе хорошо видны щели завесы.
Схема охлаждения камеры сгорания
Охлаждение камеры сгорания комбинированное наружное и внутреннее. Наружное охлаждение обеспечивается протоком горючего по межрубашечному пространству камеры, а внутреннее организовано подачей части "Г" через отверстия в стенках поясов завесы на внутреннюю поверхность нижней части КС.
Поступающее из коллектора (б) в межрубашечное пространство горючее разветвляется на два потока, один из которых направляется к критическому сечению, другой к срезу сопла. На срезе сопла последний собирается в коллекторе (а) и по перепускным трубопроводам поступает в коллектор (в) бандажа, здесь же оба потока соединяются. Далее, проходя по зарубашечному пространству цилиндра КС, горючее поступает в ФГ и через форсунки впрыскивается в камеру.
Разделение "Г" на два потока позволило уменьшить высоту зарубашечной щели на большей части поверхности камеры сгорания, что существенно снизило вес камеры без ущерба для качества охлаждения.
Горючее, которое отбирается из зарубашечного пространства подается в поясы завесы, закручивается наклонными каналами и в виде равномерной пелены ложится на огневую поверхность нижней части КС. Пелена прижимается к стенке КС набегающим потоком газов и испаряется под действием высокой температуры. Тем самым снижается соотношение компонентов в пристеночном слое газов, благодаря чему снижается температура стенки.
Сотовая труктура стенок КС. Кажется впервые такая конструкция с прокачкой горючего через стенки камеры сгорания для ее охлаждения была применена на немецкой ракете ФАУ-2. С тех пор ничего не поменялось, изменились только технологии.
Рис.5. Пояс завесы
1 - кольцо соединительное
2 - силовое кольцо
3 - кольцо распорное
4 - огневая стенка
На цилиндрической части камеры сгорания установлены два пояса завес, организующие внутреннее завесное (пленочное) охлаждение огневой стенки камеры. Верхний пояс расположен в непрсредственной близости от смесительной головки. Нижний пояс расположен перед сужающейся средней части камеры.
Отбор горючего для завес осуществляется непосредственно из охлаждающего тракта наружного регенеративного охлаждения камеры. Из тракта охлаждения жидкость поступает в каналы - круглые отверстия, тангенциально расположенные в стенке с малым шагом для обеспечения равномерности распределения расхода по периметру окружности. Кроме того, перед выходом на внутреннюю поверхность стенки жидкость перемешивается в специальной проточке, выполняющей роль выходного коллектора завесы.
Для защиты огневого днища между основными форсунками установлены малорасходные форсунки горючего.
Огневая стенка дополнительно защищена от прогара жаростойким керамическим покрытием.
Разрез стенки камеры сгорания
Газогенератор наддува бака горючего М332-00
1 - штуцер подвода горючего
2 - стопорное кольцо
3 - гайка накидная
4 - корпус
5 - форсунка горючего
6 - форсунка окислителя
7 - штуцер замера давления газа
8 - смесительная головка
9 - наружное днище
10 - трубка
11 - огневая стенка
12 - наружняя стенка
13 - огневая полость
14 - форсунка подвода балластного горючего
15 - фланец
16 - кольцо
Газогенератор наддува предназначен для создания рабочего тела - газа наддува бака горючего при полете ракеты.
Газогенератор представляет собой неразъемную сварную конструкцию, состоящую из шатровой форсуночной головки 8 и охлаждаемой горючим нижней части 13 с форсункой - разбавителем 14.
К выходному фланцу газогенератора присоединяется трубопровод наддува бака. Между газогенератором и трубопроводом установлен мембранный узел для разделения внутренних полостей двигателя и бака.
Компоненты топлива подводятся в газогенератор через штуцер 1 (горючее) и штуцер корпуса 4 (окислитель). Номинальные расходы окислителя и горючего обеспечиваются проходными сечениями жиклеров, установленных на магистралях подвода компонентов топлива.
Для обеспечения устойчивого режима работы газогенератор имеет двухзоное смешение компонентов. В зону сгорания через форсуночную головку подается весь расход окислителя и треть расхода горючего. Остальная часть горючего подается в зону разбавления через форсунку - разбавитель 14, благодаря чему происходит снижение температуры газа до заданного значения. Охлаждение газогенератора обеспечивается протоком горючего по межрубашечному пространству к форсунке-разбавителю.
Газогенератор наддува бака горючего М322-00 жидкостного ракетного двигателя РД-276. Изготовлен в 2012 г. Предназначен для создания заданного давления в газовой подушке бака горючего ракетного двигателя РД-276 ракеты-носителя «ПРОТОН».
Материал: стали 12Х21Н5Т, 12Х18Н10Т, ХН60ВТ, 15Ч18Н12С4ТЮ, 09Х16Н4Б
Технология изготовления: высокотемпературная пайка в вакуумной печи при Т = 1200 гр. С, автоматическая аргонодуговая сварка в непрерывном и импульсном режимах.
Корпус газогенератора 3Д81.05.380. 2012 год изготовления. Является частью блока розжига двигательной установки ракеты.
Материал: медь М1; стали 12Х18Н10Т, ХН60ВТ
Технология изготовления: высокотемпературная пайка в вакуумной печи при Т = 1200 гр. С, автоматическая импульсная аргонодуговая сварка, электронно-лучевая сварка в вакууме.
Использованы материалы
статьи по РД-275Все детали на фото производства ОАО "Протон-ПМ"
В пятницу будет интересное продолжение про космос. Всех причастных с праздником!
Если понравилось - ставим лайки, кидаем жетоны и тащим репртаж к себе в соцсети