Originally posted by
rvk. at
Связь Инжиниринг КБ Это тот случай, когда писать статью чертовски сложно. Даже я, инженер системотехник, по образованию, бегая между футуристично выглядящими машинами, и слушая рассказ об этом производстве, не всё понимал и сыпал вопросами. А ведь когда-то, 15 лет назад, мы в университете проходили технологию производства печатных плат. Но то ли нас тогда учили чему-то уже устаревшему, то ли с тех пор технологии сделали космический рывок, но чувствовал я себя как студент прогулявший все лекции в семестре, и решивший посетить последнюю. Поэтому так не просто рассказать о самом современном в России производстве печатных плат, находящимся на самом острее современной технологии, оснащенном самым современным и гибким оборудованием существующим в мире, способном производить любые самые сложные и передовые изделия как мелкосерийными так и промышленными партиями.
Но я попробую.
Связь Инжиниринг КБ - резидент Особой Экономической Зоны «Дубна». Всего месяц назад компания открыла на территории ОЭЗ новый, суперсовременный завод по производству печатных плат. Инициатор этого проекта ЗАО «Связь инжиниринг» - компания занимающаяся разработкой и производством радиоэлектронной и электротехнической продукции для: сотовой и фиксированной связи, телерадиовещания, радиолокации, энергетики, железнодорожного транспорта, нефтегазовой отрасли и других отраслей нашей промышленности. Компания имеет два завода в Москве и Азове, а теперь и собственное производство печатных плат в Дубне. Да какое производство!
Связь Инжиниринг КБ способен производить печатные платы до 6 класса точности (включительно) и до 25 слоев. Одним словом - самые современные из тех что есть в мире. Проектная мощность - 55 тыс.м2 печатных плат в год.
На склад компании приходят готовые заготовки для внутренних словев платы определенных типовых размеров. После чего эти заготовки отправляются на промывку.
-
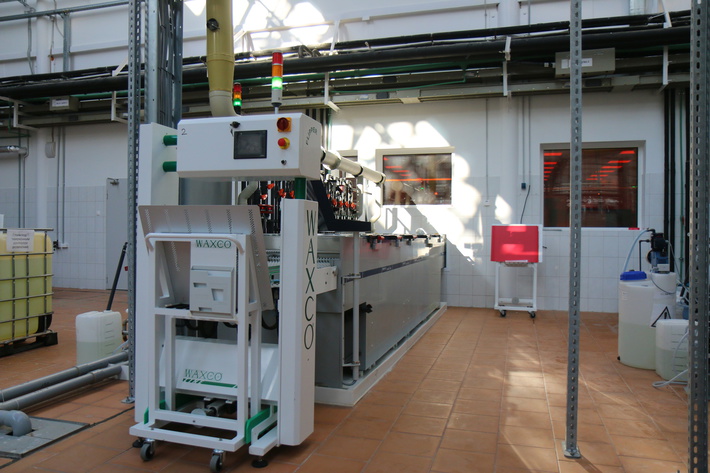
- Установка промывки
Здесь две таких установки, они абсолютно идентичны, но одна используется для промывки внутренних слоёв, в другая для промывки толстых уже спрессованных плат. После промывки заготовки заезжают в чистые помещения, где происходит операция нанесения фоторезаста.
Поэтому в чистых компнатах такой свет, что бы не засвечивать фоторезист. После нанесения фоторезиста, на заготовку наносится рисунок, часть фоторезиста засвечивается по определенной матрице, и становится нерастовримым.
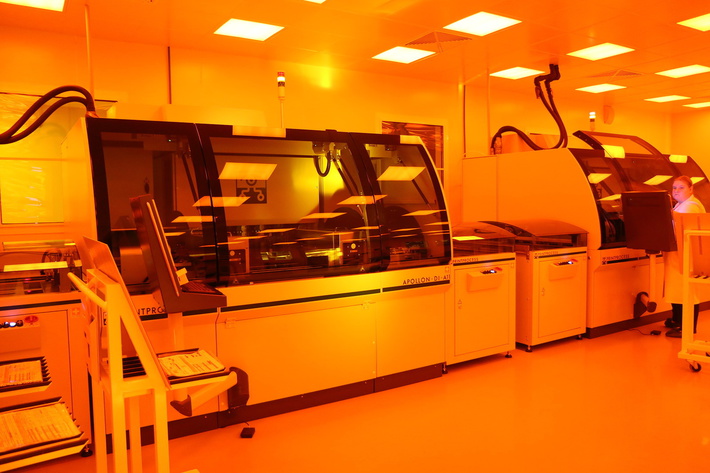
В машину загружается программа, которая управляет 4-мя головками со светодиодами, которые бегая по заготовке «рисуют» на ней заданное изображение. Это установка прямого экспонирования печатных плат. Это, кстати, отличается от того, что я знал раньше. По старой технологии фоторисунок наносился путем засвечивания фоторезиста через фото-шаблон (примерно как наши отцы делали фотографии, засвечивая фото-бумагу через негатив). Но этот способ имеет ряд недостатоков, например необходимо подготовить фото-шаблон, а это дополнительная технологическая операция. Фото-шаблоны склонны к изменению своих геометрических параметров, в процессе хранения, от влажности, от температуры, а это снижает точность операции засветки фоторезиста, а значит и ухудшает параметры изделия. В случае с прямым экспонированием этих недостатков нет. Система технического зрения очень точно совмещает загтовку с рисунком, и нанесение происходит максимально точно. Не стоит забывать, что речь идет о многослойных печатных платах, а значит рисунки на разных слоях должны соответвовать друг другу. Установка прямого экспонирования сама контроллирует это совмещение, при необходимости масштабируя рисунок, и добиваясь точного совмещения рисунков различных слоев. В случае фото-шаблонов в процессе операции ничего изменить уже нельзя. Если требуется другой масштаб то нужно готовить отдельный шаблон.
Это наиболее современная технология, массовое внедрение которой началось всего несколько лет назад. Технология позволяет не только упростить жизнь производителю, но и позволяет ему производить более качественные и более точные изделия с большим разрешением и миниатюрностью элементов.
Но у старой технологии есть и преемущество - более высокая скорость нанеения рисунка, но производительности новейшей установки хватает, для того что бы загрузить всесь завод в три смены - то есть её производительности достаточно для потребностей предприятия.
А мы идем далее, вслед за заготовкой, на которую уже нанесли рисунок будующей платы. Теперь заготовка идет на проявление фото-резиста, травление фоторезиста и снятие фоторезиста. Для этого заготовки снова загружают в установку в виде конвейера.
После всех операций, плата промывается однопроцентным раствором соды, в результатае чего, незасвеченные участи фоторезиста вымываются, остаётся только засвеченный рисунок.
Кстати, здесь, впервые в России, установлены установки регенирации травильных растворов. Нужна она потому, что в России нет компаний, занимающихся утилизацией травильных растворов. В Европе таким компаниям просто сдается отработавший раствор, и взмен выдается новый. В России об этом приходится заботится производителю. В установках извлекается медь и другие металлы, раствор корректируется по химии, и вновь используется, работая таким образом в замкнутом цикле. Здесь две таких установки, одна для кислых, а другая для щелочных растворов.
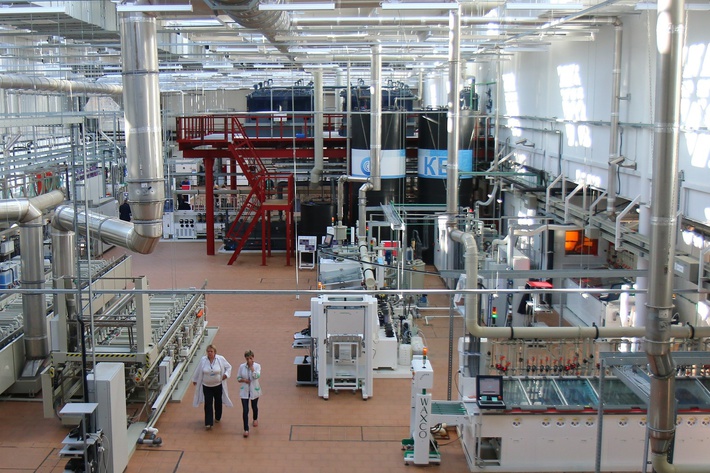
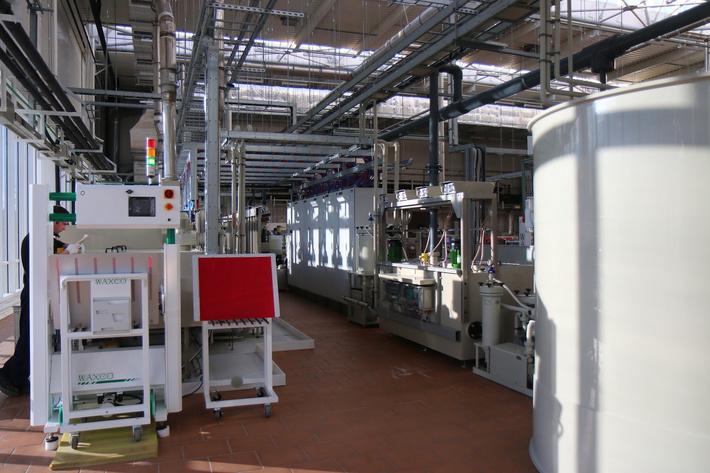
Но вернемся к нашей плате. После снятия фоторезиста, плата отправляется на операцию нанесения паяльной маски. Паяльная маска это такой защитный слой, который вы можете видеть на любой печатной плате, обычно он зеленый, хотя может быть и других цветов. Для создания паяльной маски снова наносится фоторезист, и на нем снова засветкой создается рисунок. Но на этот раз используется классическая технология заветки через фото-шаблон. Почему так? Как я уже говорил, классическая технология быстрее технологии прямого экспонирования. Так как в случае с паяльной маской не нужна повышенная точность и высокое резрешение рисунка, на первый план выходит скорость операции.
Установка совмещает фото-шаблон по специальным ремерным точкам с платой, после чего шаблон и плата заезжают внутрь, где происходит засветка ультрафиолетом.
Далее на заготовку наносится паяльная маска. Делается это двумя способами. Первый способ - распыление. В конвейерной системе заготовка в вертикальном виде проходит через систему, где специальные распылительные головки наносят паяльную маску, после подсушивания заготовка уходит по конвейеру для дальнейших операций.
Есть тут и другой - более сарый способ - паяльная маска наносится типографическим способом.
Для чего две технологии предназначенные для однй и той же операции? Для гибкости. Иногда заказчик хочет синюю паяльную маску. Что бы не перенастраивать сложную современную линию, можно использовать классическую установку, которая менее производительная, но её проще перенастроить. К тому же это резерв, на случай если что-то случится с осносной линией.
После нанесения паяльной маски, заготовки снова уходят на участок мокрых процессов, то есть на химическую обработку.
После всех химических операций и отмыки, заготоки уходят на операцию сборки слоев.
Слои перекладываются спеиальными клейкими листами, на основе стеклоткани и эпоксидной смолы, и с помощью системы технического зрения, по реперным точкам, позиционируются относитьно друг друга, потом кладется следующий слой, и операция повторяется. Посоле того как все слои собраны, этот «бутерброд» фиксируется с помощью заклепок и уходит на операцию пресования.