В последнем моём посту речь немного касалась такого аспекта как управление сцепкой тягач - полуприцеп, а сегодня мне на глаза попадается хороший материал Алексея Донского(
alexey_donskoy) о производстве автоцистерн на чувашском заводе "Сеспель", значит продолжим прицепную тему))).
"Бочка" - прицеп специфический, его не так часто встретишь на дороге как тент или рефрижератор, но и не экзотика, по типу тралов для перевозки супертяжёлых конструкций, бензовозы мы каждый день видим. Ещё, "бочек" практически не бывает частных, под такой тип груза надо специально искать работу, причём чтоб заказы были постоянны, а то простой такой техники выльется в большую копеечку. Про частные бензовозы я так же не слышал, многие бы наверное согласились, да кто ж к вентилю подпустит (а вот про хорошую жизнь водителей бензовозов я слышал неоднократно, даже знаю конкретные примеры, но это совсем другая тема).
От себя добавлю, что "бочки" бывают трёх типов: под жидкости, а так же сыпучие и газообразные продукты. Эта с виду простая сигарообразная телега таит в своих внутренностях сложную систему отсеков с волнорезами, продольными и поперечными, кому интересна техническая начинка "бочки", загляните
вот сюда.
Под катом находится подробная экскурсия по заводу с большим количеством фото- и видеоматериала от Алексея Донского.
Резервная копия на блоге
При Дороге. Оригинал взят у
alexey_donskoy в
ЗАО "Сеспель" - реальное производство на чувашской землеИтак, в соответствии с
анонсированным ранее планом мы посетили производство автоцистерн на заводе
ЗАО "Сеспель".

Завод изначально проектировался по примеру современных европейских производств. Новейшие технологии даже при небольших размерах и количестве работников около 500 человек позволяют выпускать свыше 2500 автоцистерн в год. Кстати, 1 место по Чувашии в
экономическом соревновании за 2012 год в категории от 300 до 600 человек! :)
Лозунг компании: "Немецкое качество по российской цене".
Посмотрим, как это достигается.
Во-первых, чтобы сразу было ясно: современная автоцистерна - очень сложная конструкция.
Как и обычный автомобиль, автоцистерна имеет внушительный набор средств пассивной и активной безопасности, включая антиблокировочную систему ABS и систему курсовой устойчивости.
Кроме того, свои особенности конструкции имеют цистерны для бензина и мазута, битума и зерна, муки и цемента, химической продукции, простой воды и комбикормов:
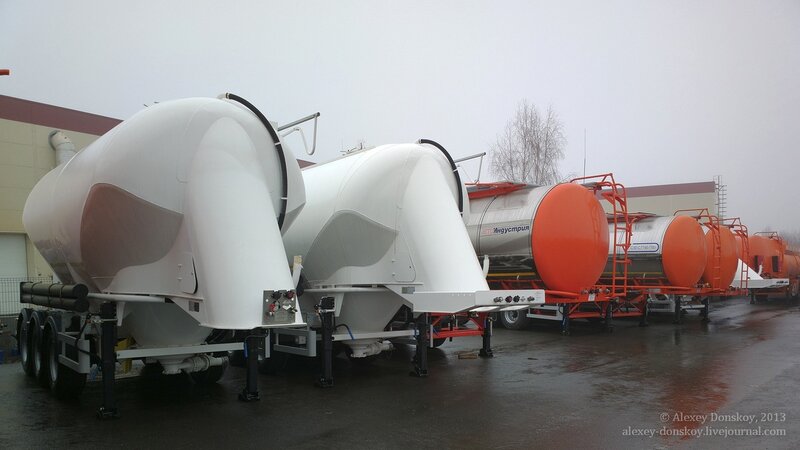

Полную экскурсию по всему производству провёл директор ЗАО "Сеспель" Владимир Бакшаев:

Присутствовал также Глава администрации моргаушского района Ростислав Тимофеев.
В этом сельскохозяйственном районе республики такой завод уникален. Впрочем, говорят, по ряду технологий и в России тоже уникален :)

Слушают блогеры
kipek,
cterra,
baryshov,
makalval и
yuriy21.
Производство начинается с раскроя листовых материалов:
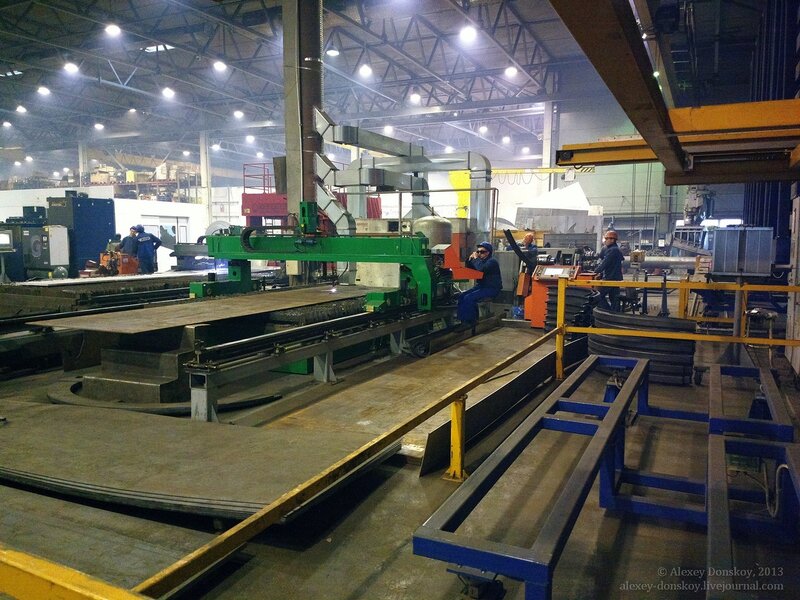
Раскрой листа классическим методом.

Лазерный станок для раскроя листового материала.
А вот и сам лазер:

Сварка в цеху везде, всеми возможными способами:
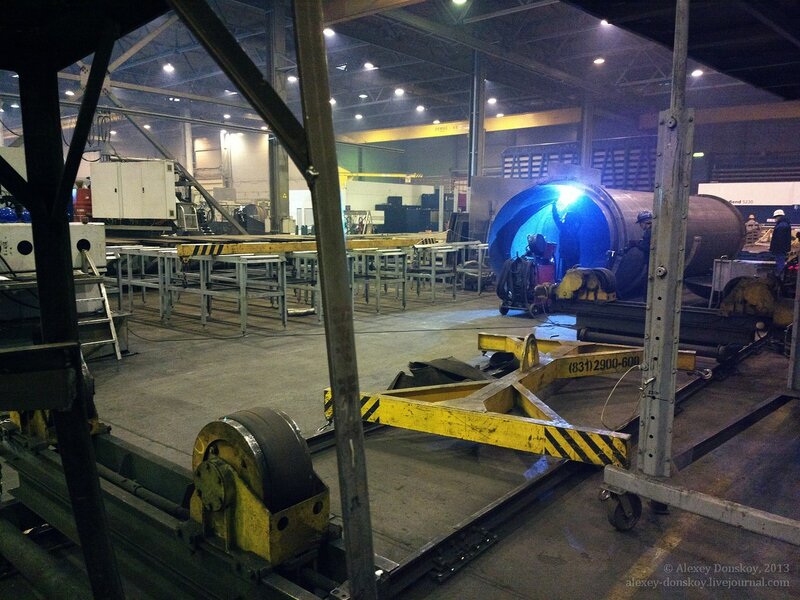
Здесь использована лазерная сварка:
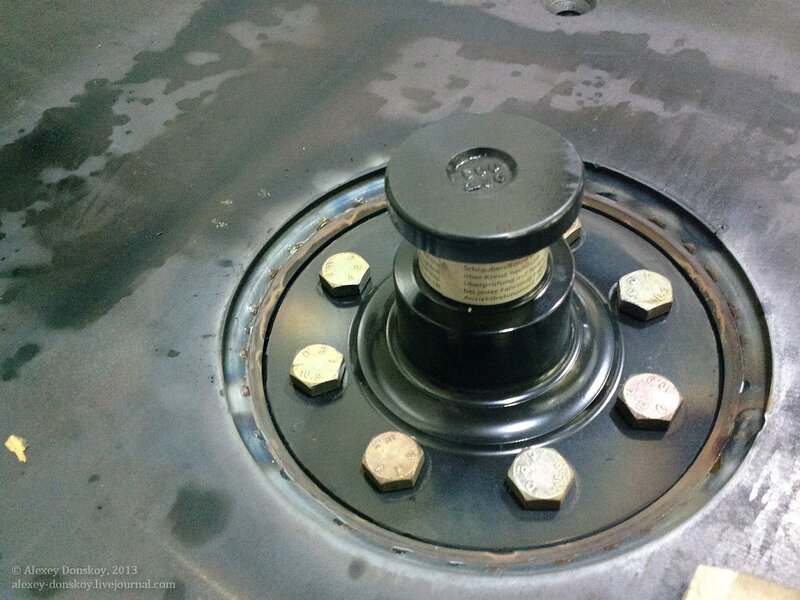
Монтируется и новый станок 3d лазерной сварки:

Робот для аргоновой сварки объёмных деталей (процесс его наладки показан ниже на видео; только, простите, на видео я его лазерным обозвал :)):

Образец плазменной сварки:

А вот и сварочный пост - хоть не робот, но оснащённый Wi-Fi (все параметры сварки задаются на центральном компьютере):
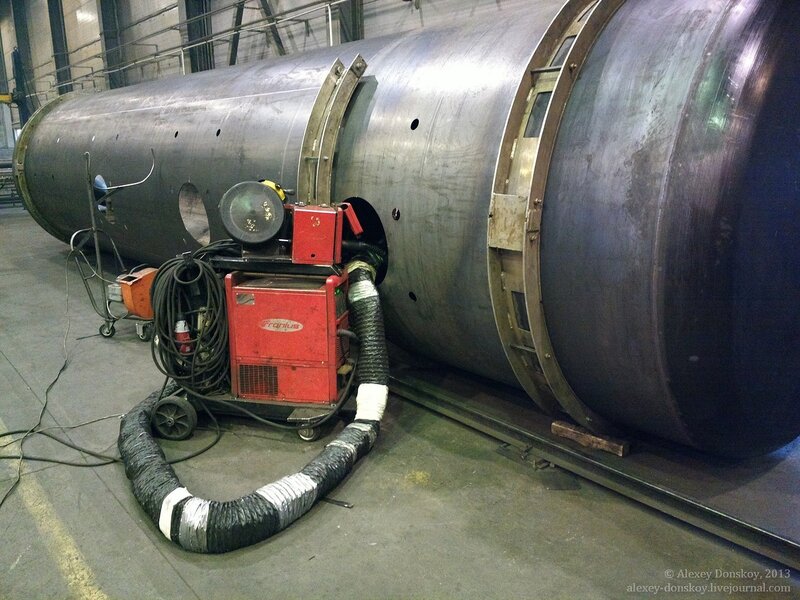

Вообще, тут большая часть операций автоматизирована, и все программы в станки и роботы загружаются по Wi-Fi. Соответственно, ничего не стоит быстро переналадить устройства на другую деталь и даже материал!
Для корпусов цистерн применяются сталь, нержавейка и алюминий.
Почему алюминий, наверное, объяснять не нужно: для транспорта вес всегда очень важен.
Но, как известно, варить лёгкий металл труднее всего: он моментально окисляется.
Поэтому раньше применяли аргоновую сварку (чтобы без кислорода). Вот такое качество шва получается после аргоновой сварки:

А вот совершенно другое качество:

Это шов после сварки трением с перемешиванием.
"Сеспель" в России является пионером по использованию такой технологии.
Здесь твердосплавный шток крутится, с усилием вдавливаясь между торцами свариваемых листов. Алюминий расплавляется и аккуратно заполняет шов, который получается ровным, без лишнего металла, и прочным, как сам лист.
Кроме того, существенно ниже нагрев металла и потому отсутствует деформация.

Работа сварочного станка показана ниже на видео.
Ещё один станок для сварки трением. Здесь свариваемые листы располагаются горизонтально:


В освоении технологии и разработке собственных инструментов для неё участвует машфак ЧГУ.
Вообще, планомерно проводится "локализация" производства, то есть самостоятельное (и потому более дешёвое) изготовление возможно большего количества оснастки и комплектующих.
Так, в цистернах-прицепах используется дорогая немецкая тормозная система Wabco:

Вот схема этой сложной системы:

Но часть её внутренностей производится уже здесь. Например, ресивер, который выдерживает даже большее давление, чем немецкий:

Пульт управления тормозной системы тоже "локализован":

Таблички с русскими надписями гравируются здесь же на лазерном автомате (см. также на видео):

А вот на этом станке лист скатывается в цилиндр:

В конструкции всех цистерн, кроме цилиндрического тела, есть ещё закруглённые торцы.
Закругление нужно для равномерного распределения напряжений в конструкции (соединения с сильно выраженными углами по этим углам обычно и рвутся):

А сделать такую "крышку" - отдельная история! Для этого есть не так много способов: литьё по форме или штамповка.
Литейного производства здесь нет; а что до штамповки, так представьте пресс для детали диаметром в 2,5 метра!
Поэтому здесь используется ещё одна интересная технология: ротационная вытяжка, то есть раскатывание круглой заготовки специальным роликом по матрице:

Есть и другие, более мелкие, детали, которые также изготавливаются этим методом:

Как работает ротационная вытяжка, смотрите на обещанном видео. Очень похоже на то, как гончар формирует кувшин на гончарном круге.
Показана в основном вытяжка мелкой детали; обработка большого торцевого элемента не так зрелищна, хотя сам станок впечатляет!
Click to view
Кстати, кроме обычных круглых, освоено и производство овальных торцевых элементов (на следующем фото один такой сзади виднеется).
Догадайтесь, как это делается? ;)

Внутреннее устройство цистерны непростое. Это снаружи она выглядит блестящей бочкой, а внутри даже чисто по конструктиву есть масса деталей: переборки, рёбра жёсткости, многослойная теплоизоляция. Для теплоизолированных цистерн продуманы специальные конструкции, чтобы убрать возможные мостики холода.
На следующем фото видна изоляция и наружное защитно-декоративное покрытие:

Ну а далее используется куча дополнительного оборудования: от загрузочных люков до дисковых кранов, от компрессоров до сливных шлангов, размещаемых рядом с корпусом цистерны...
Да, если используется теплоизоляция, то требуется ещё одна деталь и, соответственно, ещё одно вспомогательное производство: наружных торцевых элементов.
Они, разумеется, уже не металлические, а пластиковые:

Технология похожа на производство акриловых ванн:

Армирующие волокна заливаются связующим и уплотняются вакуумной "присоской":

После сборки основных конструктивных элементов цистерну (особенно стальную) необходимо ещё и покрасить.
Сначала красили вручную:

А потом обзавелись специальным покрасочным роботом:

Автоматизированная покраска по качеству такая же, как и у автомобилей. Кроме того, по сравнению с ручной работой краска расходуется гораздо экономичнее:

Как вы уже видели, автоцистерна представляет собой многоосный полуприцеп, который присоединяется к стандартному грузовику.
Соответственно, она имеет все необходимые автомобильные части.
О надёжной тормозной системе мы уже говорили выше, теперь пара слов о подвеске.
Комплектование подвески тоже автоматизировано, производится по VIN-кодам:

Используются только комплектующие высокого качества, например, оси BPW ECO-Plus 2 (Германия):

Устанавливается также дополнительное оборудование по спецификации заказа, например, "чёрный ящик" с поддержкой GPS и ГЛОНАСС.
Он позволяет посмотреть весь путь и момент аварии. Нам рассказали историю о том, как прислали по рекламации цистерну с погнутым носом. А чёрный ящик показал, где и когда водитель на перегруженной машине не выдержал скоростной режим и допустил удар, зацепив рельсы на переезде.
Но анализом аварии польза от "чёрного ящика" не ограничивается. Поскольку многотонный бензовоз есть особо опасное транспортное средство, необходимо тщательно подбирать персонал и контролировать качество вождения. И для этого теперь есть объективный критерий и средства измерения.

Красавец!

А ещё на топливозаправщиках устанавливается компрессор. На предприятии также разрабатывается собственная конструкция компрессора, вдвое легче зарубежных аналогов.
Да, надо также сказать о больших проблемах, с которыми сталкиваются как производители, так и потребители (скупой платит дважды).
Во-первых, это обилие дешёвой китайской продукции, которая удешевлена и облегчена за счёт безопасности. Нормальный же производитель делает необходимый запас прочности (а это "лишний" вес и цена) - и проигрывает конкуренцию.
Поэтому инновационные технологии жизненно важны для производителя!
Во-вторых, это огромные масштабы импорта дешёвой б/у техники.
Если производитель выдерживает все строгие стандарты (а они в России строже, чем в Европе), и за их несоблюдение можно остановить производство и вообще лишить лицензии, то никакой Ростехнадзор не контролирует импорт. Не проводится даже радиационный контроль (а кто знает, что возили в импортных цистернах?).
Вот так и выживает отечественный производитель.
Рентабельность производства редко превышает 6%, тогда как рентабельность капитала того же Сбербанка - 20%.
Да и торговать выгоднее, чем производить. Было бы вот только чем торговать!
Хорошо, что промышленность у нас всё-таки есть!
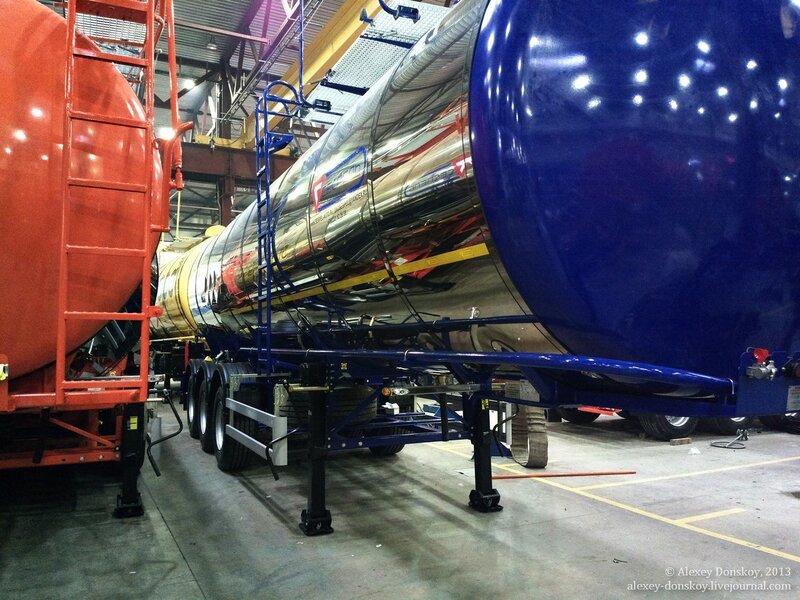
Да, а ещё мы видели машинную мойку полов, что не лишне на тонком производстве:

Посмотрев все стадии производства автоцистерн, обратим внимание на отходы.
Алюминиевые обрезки переплавляются и отгружаются на переработку производителю:


Также могут выполняться сторонние заказы - получается дополнительное литейное производство:


Кстати, тигель для плавки алюминия должен быть только керамическим:

Есть и другие вспомогательные производства, например, газоподготовка, очистные сооружения, лаборатория, где постоянно контролируют образцы сварочных швов; наконец, есть собственное конструкторское подразделение, результаты которого по безбумажной технологии передаются прямо на станки и роботизированные комплексы.
Вот такое замечательное производство есть у нас, можно сказать, в сельской глубинке.
Поздравляю коллектив предприятия с 25-летним юбилеем!
Работают здесь местные жители, а все окрестные школьники обязательно бывают на экскурсии.
Владимир Александрович постоянно говорит о работе с молодёжью, о необходимости показывать им заводы, промышленность, реальное производство - и делать его выгодным и привлекательным для людей, в противовес нынешней всевластной и непроизводительной торговле.
Потому что человек на то и человек, чтобы ДЕЛАТЬ что-то новое и полезное!
Другие материалы по теме:
•
Подробнее о технологиях на сайте производителя Посты блогеров по теме:
•
kipek:
"Сеспель"•
yuriy21:
Наши полуприцепы! Мои посты о промышленности и энергетике:
•
Как делаются бульдозеры (Промтрактор, Чебоксары)
•
Экскурсия на Чебоксарскую ГЭС•
Освещаем космос лампочками (про Центр энергоэффективности, быт и энергетику)
•
Школа гидроэнергетика: надо ли поднимать уровень Чебоксарского водохранилища?•
ОЖДХ - что это такое? :)